We still have a couple of weeks until the holiday season, but here’s an early gift for you: I’m excited to announce our brand new Original Prusa MINI, a smart and compact 3D printing workhorse with all the bells and whistles you’re accustomed to when you buy an Original Prusa 3D printer. While we know that many of you have been calling for a larger printer, we think the MINI might surprise you and this article may have some additional treats at the end! The MINI has a print volume of 18×18×18 cm (7×7×7 inches), removable spring steel bed sheets, networking with ethernet and optional Wi-Fi and it’s all controlled by our brand new custom-made 32-bit Buddy mainboard with silent 2209 Trinamic drivers. The icing on the cake, we managed to do this (and more) for 349 USD / 379 EUR (VAT incl.)!
New compact workhorse
A bit of a backstory: During the last 10 years of making 3D printers, I have come to realize there will never be a single universal “almighty” machine. I like the idea of what’s currently happening in the field of computer processors, especially ARM with their big.LITTLE architecture. A couple of big, fast, power-hungry cores that do the heavy lifting when it’s needed, and many little efficient ones for taking care of mundane tasks. So how does the $349 Original Prusa MINI fit into this scheme?
Our goal was to make an ideal mix of streamlined and simple, compact and capable. And the MINI is the result: a printer we wanted and needed for ourselves. Our print farm is a great example of where the MINI can stand out.
First of all, the print area dimensions are 18×18×18 centimeters or 7×7×7 inches. The printer itself has a small footprint of 33×37 cm (13×14.5 in) and it’s 38 cm (15 in) tall. It requires a little extra desk space of about 35×45 cm (14×18 in) for correct operation since there needs to be some leeway for cables. This means you can easily fit several of these machines on a single shelf and run them simultaneously, producing a large number of high-quality objects at a rapid pace. Don’t like waiting for a print job to finish? Run three or four printers at the same time and get your results much faster! To make this even more efficient, we plan to implement our print farm management software in a future update.
One of the problems with large-format 3D printers is the fact that print jobs usually take dozens of hours – and if, for whatever reason, the print fails after three days of non-stop operation… well, it’s pretty painful.
This little machine is capable of doing some great things – no matter whether you want to set up a small printer farm, make accessories for cosplaying, print miniature figures for desktop RPGs, or produce prototypes and mechanical parts from PETG, the MINI can do it with minimum hassle. After a fast minimal assembly, you’re ready to print.
With the MINI, you’re getting everything that has made our printers popular worldwide: fully tested parts with a warranty, a detailed assembly guide, and 3D printing handbook tested print profiles in PrusaSlicer, 24/7 tech support in seven languages, firmware updates… and there’s, of course, the massive community that can help you with both the basics and advanced 3D printing topics. We also have our safety features in place – three thermistors, power panic and more. All of which makes the MINI an ideal first 3D printer – not only for individuals, but I imagine it will be very attractive for classrooms as well.
Smart with plenty of features
As I already mentioned, the price of the Original Prusa MINI is 349 USD / 379 EUR (VAT incl.). So what did we manage to do with such a tight budget?
Essentially, we went back to the drawing board and did something similar to what I had done with the i3. Back then, I took something rather complicated, which was then seen as a standard, and turned it into something much more streamlined. Yeah, you might say that the MINI looks like it’s missing some parts. Trust me, the same happened with the i3 design – and it became a huge hit.
Of course, the MINI isn’t just a smaller version of its older brother, it adds quite a few awesome features that are new to our family. It has a full color LCD display (2.8’’, 320×240, 65k colors), replaceable spring steel sheets (you can choose between smooth and powder-coated!), print via ethernet, optional Wi-Fi, or direct from USB drives (no more SD cards), Mesh Bed Leveling, support for E3D nozzles, sensorless homing thanks to silent Trinamic 2209 drivers, custom 32-bit mainboard, built-in online firmware updater… And we’re improving the user experience as well.
The MINI comes standard with “One-Click Printing” – insert a USB drive with a sliced object and then you’re just one click away from starting the print! And the rest is pretty quick, too! Preheating the machine for PLA printing takes roughly a minute, while ASA preheat is around 3 minutes – depending on the ambient temperature, of course. Plus, you can swap the nozzles with other E3D compatible nozzles. The standard 0.40mm nozzle is a great, versatile solution, but if you need highly detailed prints (e.g. miniatures for your desktop RPGs), you can easily swap it with a 0.25mm to achieve a higher level of detail.
You can inspect the detailed specs below:
ORIGINAL PRUSA MINI | ORIGINAL PRUSA i3 MK3S | |
Build volume | 18 x 18 x 18 cm | 7 x 7 x 7 in | 25 x 21 x 21 cm | 9.84 x 8.3 x 8.3 in |
Layer height | 0.05 – 0.35 mm | 0.05 – 0.35 mm |
Max travel speed | 200+ mm/s | 200+ mm/s |
Max hotend/heatbed temp. | 280 °C / 100 °C (536 °F / 212 °F) | 300 °C / 120 °C (572 °F / 248 °F) |
Mainboard | Custom 32-bit Buddy electronics with STM32 and latest Trinamic 2209 silent stepper drivers | Einsy RAMBo 8-bit board with Trinamic 2130 drivers co-developed with Ultimachine |
Extruder | Bowden system with 3:1 gearing | Direct drive |
LCD screen | 2.8″ graphic 65k color screen | Monochromatic LCD |
Print surface | magnetic heatbed with removable PEI spring steel sheets | magnetic heatbed with removable PEI spring steel sheets |
Filament diameter | 1.75mm | 1.75mm |
Nozzle diameter | 0.4mm (default) / other nozzle diameters supported | 0.4mm (default) / other nozzle diameters supported |
Supported materials | PLA, PETG, ASA, ABS | Any thermoplastic including Nylon and Polycarbonate |
Filament sensor | Optional upgrade | Yes |
Power panic | The future software upgrade, single layer accuracy | Hardware-based, single G-code line accuracy |
Ethernet connection | Yes | Via Raspberry Pi |
Wi-Fi connection | As a separate future upgrade | Via Raspberry Pi |
MMU2S compatibility | No | Yes |
Advanced sensors | 3 thermistors, fan RPM sensors | 4 thermistors, fan RPM sensors |
Farm mode | Yes, built-in (upcoming feature) | Yes, with additional HW |
Calibration | Automatic, Mesh Bed Leveling | Automatic, Mesh Bed Leveling |
Print medium | USB drive / LAN | SD card |
Firmware update interface | USB drive / LAN | USB port |
PSU | 160W, external adapter by Meanwell or Delta depending on the region | 240W, custom made by Delta with Power Panic HW |
Kit price | 349 USD / 379 EUR (VAT incl.) | 749 USD / 769 EUR (VAT incl.) |
Assembled printer price | – | 999 USD |
So, here we are, once again on our way to turn something that might be seen by many as a very complicated machine into something that is getting closer to a home appliance. This is also reflected in the assembly process: we decided to launch the MINI as a much more simplistic “assembly kit” – you just put three pieces together and then you’re ready to print in less than half an hour.
In the end, we were pretty much surprised to see how many boxes the MINI ticked. To keep the price down, we decided to make the filament sensor an optional upgrade, while the power panic will come later as a free software update. Sure, the build volume is smaller, the power supply is an external adapter and the Wi-Fi will use a small cheap ESP board you can source yourself from any good electronics shop. However, there are so many things squeezed into the very tight price point of 349 USD we could not believe it ourselves. 🙂
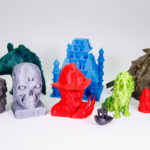
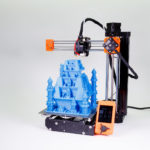
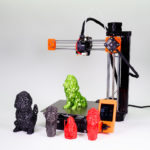
The Prusa i3 heritage
Wait a second, does this mean that the MINI is like a video game console with no means of tweaking, tinkering or modding? Not at all! It’s still an open-source machine and I can’t wait to see what our community will do with it. In fact, we’re giving you some rather powerful hardware to play with.
This time, we’re using our own custom-made 32-bit mainboard called Buddy. It’s based on an ARM STM32F407 chipset, it features RTOS (Real-Time OS), silent Trinamic 2209 drivers, ethernet port, ESP support (for the optional Wi-Fi module) and it will support our farm management software natively in the future. It allows us to run things in parallel – one thread is reserved for Marlin 2 (motion planning), the second thread is for LCD GUI and the third one is for networking. Basically, everything you can achieve with OctoPrint can be done on this mainboard as well – even a camera connection (although it runs at 1 fps)! Not every feature will be available in the launch firmware, but we will keep improving the printer through new firmware after launch.
Why did we decide to switch to a 32-bit board? Surprisingly, raw performance is not the main reason. We can now write cleaner and more abstract (reusable) code without assembler hacks like on the 8-bit board. Adding new features becomes much less of a hassle and we don’t have to count every single byte in the flash memory. Unit tests and JTAG debugging sped up the development and we also got the chance to include ethernet and optional Wi-Fi connections.
The new 32-bit board will also allow us to bring you our sophisticated print farm management software in the future. You often ask us, how do we manage 500 3D printers running 24/7 – smart management software is the answer. It’s something our community has been asking for a lot. We’re working on it – it will take some time to make it user-friendly, though.
When you take a look at the machine, you will certainly recognize many familiar parts – we’re using long-time proven components for maximum reliability, something you would expect from our printers. However, there are some slightly different bits: since we’re using a streamlined design for the X-axis (the “arm”), we made the extruder a lot lighter. However, this also means that the MINI is not compatible with MMU2S. The extruder motor is now located on the vertical column and it feeds the filament with a 3:1-ratio drive gear through a PTFE tube into the hotend, which moves along the X-axis.
A large printer, you say?
So, as you can see, the MINI can do a lot. However, if you are one of those who need a large-format 3D printer (and you managed to read all the way through), here’s the news for you: we’re working on a little something you may call a “Prusa XL”. Expect a print volume of 40×40×40 cm and a lot more! This won’t be merely a bigger MK3S – using the same design would bring way too many issues (heavy heatbed, less stability with higher Z-axis values). Instead, we plan to base the XL on CoreXY architecture. It will feature a new geared extruder and an improved heatbed – among other things.
Quite a lot of news for just one article, right? 🙂 Well, we still have something else. “What about the i3 line and the MK3?” you might ask. Is it now outdated? I assure you it’s not. We’re still deep in development of the XL (CoreXY) 3D printer and it’s quite possible that some of the best features of both new printers will find their way to the good ol’ MK3 in a form of an affordable upgrade.
In other words: the MINI isn’t meant to replace the i3 MK3S product line. It’s a different kind of product and we don’t plan to discontinue the MK3S anytime soon – there’s still room for potential upgrades. We’re definitely not going to announce another new printer this year. The MK3S in the current form is better than ever and it is in-stock with both steel sheets variants.Model by Arte Creator
A printer for everyone
So here’s my vision, returning to the big.LITTLE CPU analogy: imagine a workplace with two large XL printers, a couple of MK3S machines, a number of MINIs and an SL1 – every printer has its place and purpose, allowing enterprises and individuals to achieve their goals in the most efficient ways.
The MINI is an awesome starting printer for pretty much anyone! Whether you are a cosplayer, hobbyist, or just curious about 3D printing, the MINI has you covered. Do you want to print something large? A piece of armor for your cosplay? Since printed costume parts usually need to be post-processed (sanded, painted), you can easily print a larger object separated into several parts and glue everything together afterward. Fillers and paint will hide the seams. Do you need a set of figures for your desktop RPG? Replace the 0.4mm nozzle with a 0.25mm model and you’re all set! Does your client require a number of mechanical parts printed with PETG no later than tomorrow? Set up a small print farm with a couple of MINIs and let them produce dozens of parts in parallel!
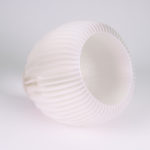
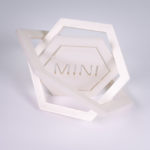
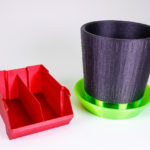
So don’t forget to check out the product page and the store page. And if you’re at East Coast RepRap Fest, stop by at our booth and see the MINI with your own eyes. Or, of course, you can take a look at MINI on all upcoming events promoted on our website. It’s small, but it can do some mighty things!
Happy printing!
Christmas came early 🙂 Quick question about the mini:
Will this printer do well (survive) as a “travel printer” that i can bring with me on stands, demo´s, vaction etc?
Sounds awesome!
Any chance the new Buddy board will be adapted as an upgrade for the MK3S?
I asked someone at the booth about putting a buddy board and the new interface on a MK3S and they said that there aren’t any current plans, but seemed to be a little confused at first talking about upgrading the MK3S to a MK4, so maybe that will be at least part of what an i3 MK4 would be.
But once the initial rush for the Mini (and production can keep up with the demand) the buddy board and screen will show up in the stores for us to try unofficial mods to integrate the two. (But, we the community, would probably be responsible for the firmware updates so the buddy board is thinking it is connected to a larger print volume and direct drive.)
The power connector is totally different as well, so I wouldn’t try using it.
I can see ways of transferring so many of theses features over to the i3 but it would be so big an overhaul it wouldprobably be more of an i4 rather than an i3 Mk4.
Relocating the extruder motor from the x carrage would lighten up the extruder a lot.
I really want to see a great overhaul on the i3 but I’d imaging an upgrade kit would be pretty pricey, but hey If Prusa want to make it I’m willing to be a tester for them 😉
I’d rather the weight of a direct drive extruder rather than Bowden. Bowdens are great but my last printer I could never get it dialed in to stop oozing so love my MK3S!
Even if a future i3 upgrade didn’t have the bowden, I’d really like to see the new board with wifi/ethernet and a colour side mounted screen/control.
The front mounted display always bugged me
Wird es das Board und das Farbdisplay als Upgrade auch für den MK3S geben?
This is just what I needed. Smart move by Prusa. I still have my workhorse MK2.5s and I couldn’t justify the cost of an MK3 since it’s just marginally better than the MK2.5 and still running an 8bit board. I’ve had Railcore on my mind but I may wait for Prusa’s CoreXY which will replace the MK2.5. The mini fits in perfectly although it stole the funds I was going to use for the Elegoo 🙂 Having the mini planted right on my desk will allow me to still use my MK2.5s for customer prints while having a spare to print those important objects that you realize you need an hour after starting a 15 hour print for a customer 🙂 Pre-ordered as soon as I watched the video and can’t wait for this little printer to ship. Best of luck with this Josef.
Considering the price for the United Kingdom it’s dreadfully expensive . Also considering that some of the items are optional extras, once you add rhem it’s difficult to say what the final price will be.
Not your fault I suppose giving the state of the exchange rate.
Does it have silent mode?
Mini should be a very cost effective little workhorse, but not really very little, at 18 cm! Little cost, though. I can imagine having one just for 0.25mm work.
The upcoming 40cm Prusa printer is very interesting, but I’m not sure I would go for it for my personal use, over my MK3S/MMU2S. Now then, if it will have a tool changer, then it’s shut up and take my money time.
Great news!! I really wish that I could have a Mini right away for an exhibition in Leipzig that I will attend from 24.-27.10. I will be showcasing 3D printing. I bought a MK3S for the event because I wanted a portable 3D printer that you can rely on. But the Mini would be even better. I guess I would gain a big amount of new customers
Im just hoping my MK2S can get things like the USB interface. No more SD cards as mine keeps slipping. Mid print it’ll stop saying card removed. The rest would be cool, but USB is to of my list currently
No option to purchase as cheaper kit instead of partially pre-assembled? 🙁
The i3 MK3 was my very first printer and in retrospection I have to say purchasing the kit instead of pre-assembled had more advantages than just saving some money. Building and calibrating the machine myself has taught me a lot about how this thing works, and that knowledge has helped me tons when troubleshooting. A newbie buying a preassembled 3D printer because he is too lazy to build it will probably throw the printer into the trash the very first time it starts malfunctioning…
A big WTF to me: Switching to a big color LCD but still keeping the rotating knob control? If you’re already ditching the cheap B/W 4-line display, why not go for a touchscreen?
I’m still waiting for a dual-extruder printer from Prusa. Like one with two separate hotends. I’ve bought, tested and dumped the MMU kit as it’s just too fragile and, more important, slow as hell. If I want to color my print painting it in postprocess is a much cheaper, faster solution – but there is no good alternative to printing with soluble supports should your model require them. I don’t necessarily need that with a yet bigger build volume than my i3, although I’m afraid adding another hotend to the i3 design in a fictious upgrade would reduce the build volume to unacceptable levels.
Waiting for more info on the Prusa “XL”!
You might want to revisit the MMU2 (assuming you meant that and no the original MMU) now that the S update is out. I personally have never had an issue with my MMU2, but I have heard from those who have that it helps. There are some selector mods that can also assist in reliability.
While I agree a kit would be nice for the Mini, as an educator I appreciate the easier assembly. Lots of groups I’ve worked with assembled their machines improperly and had issues, and this allows lower packing fees while maintaining reliability (I imagine this machine might be more sensitive to assembly issues like the MMU2).
As far as dual extruders, I’ve found them less reliable, or at least more annoying. Calibrating height and distance, preventing cross-contamination, and ensuring reliable extrusion is difficult on two nozzle machines. Plus you don’t get the large number of selections like the MMU2. I could see an e3D tool-changer working well, but I personally hope that a new Prusa machine would not use a traditional two nozzle setup, or at least not two nozzles on the same carriage. We shall see I guess.
Actually I would like the idea of a “real” kit without any pre-assembly. I got my mini 1 month ago and already had two problems because of errors in pre-assembly:
– “often clogging”-problem: The heatbreak was not perfectly inserted, so the mini clogs often (but I will change the to the bondtech heatbreak anyway)
– the display case was not well cleaned from stinging in factory. Stringing wind up on the encoder and the knob did not react to pressing anymore. After disassambly and removing the stringing everything worked well again.
As a private customer time is not money, so assembly everything can be done much slower and more carefull.
Also a kit without plastic parts would be even nicer. In a printer farm, printing is done quite fast. If the mini is your second (or third or 20th) printer you can print all plastic parts yourself, in slower mode and less layerhight (more print quality) – and in the colour you want. Also it would be cheaper – and maybe with less waiting time for delivery.
Questions to Prusa:
– What will be included in the package, aside from the printer? E.g. tools like pliers, allen keys etc.? I would expect the Mini’s design to be open (hence user-repairable/modifiable) just like the i3 – at least it obviously has a lot of 3D printed frame parts – and tools are needed for maintenance. The shop page gives zero details about that.
– It appears that the 3-part half assembled design with 30 minutes of assembly time (as advertised) allows for an use case where you could disassemble the printer and stow it away in a very compact way whenever you’re not using it, e.g. when you have no personal space and only scarce shared space at home. What are the dimensions of the packaging?
– Do you have a rough estimate about when you can present more details about the Prusa XL? Still sometime this year? Next year?
A big yippee from me. I ordered one.
I guess I know what I am buying myself for Christmas this year.
Mmm better start setting aside some money for the future XL, I definitely want something bigger than even the current mk3s, so will definitely have an eye to it when more details are announced.
What about weight compared to the MK3S? Would be interesting for transport purposes for show and tell in schools etc. 🙂
Presumably software-Power-Panic is something along the lines of the Creality style “write to SD to preserve location” and cannot lift the head when power goes out because it has no way of knowing when the power goes out like the hardware based solution does.
Is there a timeline for the XL? I would love one for work. I’m currently looking for a larger one. Depending on timeline I would rather wait for the Prusa! I love my MK3S!
Super exited for the Prusa XL Printer, can’t wait for it. 😀
Hey if Josef is reading is it possible to buy a Prusa Mini as a kit like the i3 mk3?
Very impressive. The rig may even be strong enough to support multi-material extruder like QuadFusion.
Prusa should consider distributing the MINI’s touchscreen separately as well, so users can upgrade your other printers.
Can’t wait to see the Prusa XL. CoreXY is the way to go. Add linear rails or at least the option to add them for a premium price. I would totally buy it. I love the E3D Toolchanger but it is way more than I really need so not really justifying the expence. Oh and don’t forget to add support for the MMU2s eventually 🙂
Any time schedule on the Prusa XL? I need a bigger printer now, and depending on the time table I rather wait for the Prusa XL than buy, say a Crealiter CR-10 Max.
I ordered the Mini because I need a printer with a small foot print but as that is one of my main drivers I have a question about the filament holder. From what I can see in pictures it looks like there is a roller type holder for the filament spools and a small bowden tube between the spool holder and the extruder. This all looks good for me as the filament spool doesn’t need to be placed above the extruder because it feeds from the bottom, so the question is – how fussy is the placement of the filament spool holder? Again in the pictures I’ve seen it looks to be slightly to the back side of the printer, I’m just trying to figure out how much depth I will need.
If I pre order now will I be charged now or will I be charged when it ships ?
@valence28: You are charged immediately when you order. Even if you pay via credit card.
Can you guys please post the “Prusa Mini Max Cube” STL (and if possible also the other Mini files) on prusaprinters.org?
Many thanks!
Hi,
Is there any information how noisy this thing will be? Talking about the fans.
BR
Why doesn’t the mini support TPU? The hotend/heatbed seems to be capable. The material limitations is a concern for me.
This loks really great, but I must say the most exciting part of this post is the XL. I know this might be out of the question ($$$) but do you plan to add toolchanging to the XL? If so, please make it an upgrade, that would be the top of cheap consummer 3d printing.
Also, I know that this whole comment sounds like its about toolchanging, but that is probably the future. I do not know if this is possible, but a toolchanging upgarde would also be awesome for all of us MK2/3/s user. Perhaps taking the plate that has been devloped my E-3d, and mounting it on the top of a tool. This could then doc at the top, and inserted by moving the x axis. See this drawing.
https://docs.google.com/drawings/d/1cqvn1mBQJR0OfTA8bBylfjOeOAroUzLkhAVMk0Ku8BE/edit?folder=0AL5ag9P958YkUk9PVA
Awesome printers 😉
The Original Prusa MINI is a good and affordable 3D printer in a closed packed body with an end number of features and advantages. It is outstanding for start-up businesses and the fanatics across the globe.
facebook
Bude i nějaká podpora tiskárny MINI, nejlépe v češtine? Proslýchá se, že Prusa je původem Čech.
I can say for sure that such innovations are now very necessary, as well as business solutions, because many businesses still have manual, without automated management and solving complex problems. That is why I recommend to study the salesforce implementation plan and use this knowledge to configure and implement Salesforce in your company’s robot. I think it will be most useful now and there are few places where you can get such knowledge. Good luck.
A 3D printer is a functional device for layer-by-layer reproduction of a selected object. There are several basic technologies for building products, on which the type and cost of a 3D printer actually depends. The simplest techniques used in home appliances are SLA 3D printing, or stereolithography, and FDM 3D printing. The latter is the most common and is the bulk of compact 3D printers. I work as an engineer and do 3D modeling, namely providing services to clients from the engineering marketplace of Engre.co, where an interesting article was recently published about how global companies respond to the war in Ukraine. This is a functional, accurate and simple technique that can be used for many different tasks. This makes FDM 3D printers especially popular with users around the world.