L’impression 3D d’une guitare électrique a toujours été un de mes rêves, mais cela semblait être une tâche ardue. Le corps craquerait-il sous la tension des cordes ? Se courberait-elle avec le temps ? Aurais-je besoin d’utiliser des micros actifs spéciaux ? Le corps en plastique produirait-il un son affreux par rapport au bois dur traditionnel ? Il y avait tellement de questions et étonnamment peu de réponses à trouver en ligne.
Je ne suis pas le premier à tenter cela, bien sûr. Il existe plusieurs articles et modèles disponibles en ligne, dont certains modèles se révèlent très bien. Cependant, bon nombre de ces guitares imprimées n’étaient pas vraiment jouables, et certains projets qui avaient l’air bien ne partageaient pas le modèle 3D, manquaient d’instructions, étaient trop compliqués ou étaient trop chers.
Et donc la décision a été prise – je vais concevoir ma propre guitare électrique imprimable en 3D à partir de zéro.
Priorités de conception
Pour comprendre le processus de réflexion – je concevais la guitare en pensant à la communauté de l’impression 3D. Je veux que les autres puissent facilement suivre cette construction et créer leur propre super guitare. Donc, avant de commencer à concevoir quoi que ce soit, j’ai dressé une liste de priorités :
- Le projet devrait être simple
- Pas d’assemblages compliqués de dizaines de pièces, facile à assembler
- Pas de tiges métalliques pour le renforcement ou autre matériel non essentiel
- Elle devrait être bon marché, si je dépense beaucoup d’argent pour une guitare, j’achète une authentique Fender ou Gibson
- Le matériel doit être facile à trouver avec expédition dans le monde entier
- Toutes les pièces doivent tenir sur l’Original Prusa i3 MK3S+ (25×21×21 cm)
- Cela semble être une limitation très difficile, mais si elle n’est pas imprimable sur une imprimante de la taille d’une MK3, la plupart des gens ne pourront pas l’imprimer.
- Elle devrait bien sonner et être au diapason sur toute la gamme, je ne veux pas créer un gimmick en plastique injouable
- Elle devrait avoir l’air incroyablement cool !
Faire simple
Dès le début, la principale préoccupation était la force que les cordes appliquaient sur le corps et le manche de la guitare. Bien que les sources diffèrent légèrement avec les informations à ce sujet, le consensus semble être qu’elle est d’environ 50 kg de charge, en fonction du tirant des cordes (épaisseur). Ces 50 kg essaient de plier la guitare en deux, d’arracher le chevalet du corps et de courber sévèrement le manche.
Résoudre le problème du manche était honnêtement une décision sans prise de tête – je vais utiliser un manche en bois véritable. Bien que vous puissiez affirmer que la guitare ne sera plus « entièrement imprimée en 3d », le manche est une partie si essentielle et délicate de l’instrument que cela compromettrait l’ensemble du projet si je voulais l’imprimer (même si cela est possible). Les manches en bois sont parfaitement lisses et droits, ont des frettes métalliques résistantes à l’usure et ont une tige de renfort à l’intérieur, qui sert à régler le relief (arc concave ou convexe).
Résoudre le problème du chevalet nécessitait cependant plus de réflexion. Le chevalet d’une guitare électrique est une petite pièce métallique qui maintient l’extrémité inférieure des cordes. Il est généralement fixé au corps avec quelques vis. Si nous examinons les designs de guitare les plus courants, l’un des chevalets pourrait vous sembler exceptionnellement adapté à une guitare imprimée en 3D. Pouvez-vous deviner lequel est-ce ?
Tous les modèles de guitare courants sauf un ont un très petit chevalet, parfois maintenu en place uniquement avec 2 vis. En revanche, le chevalet de Telecaster, c’est une autre histoire ! Cette grande plaque de métal maintient non seulement les cordes inférieures en place, mais intègre également le micro inférieur et possède jusqu’à 5 trous de montage avec des trous de vis largement espacés, permettant une meilleure répartition de l’effet de levier sur le chevalet sur toute la plaque métallique et la pièce imprimée sous-jacente.
De plus, la Telecaster n’a qu’ un micro supplémentaire, ce qui facilite le câblage et le design. Et enfin, les boutons de volume et de tonalité, ainsi que le sélecteur de micros, sont tous montés sur une autre plaque métallique et fixé au corps avec seulement 2 vis. Cela simplifie énormément le projet, car nous n’aurons pas à intégrer individuellement plusieurs boutons et sélecteurs à la guitare.
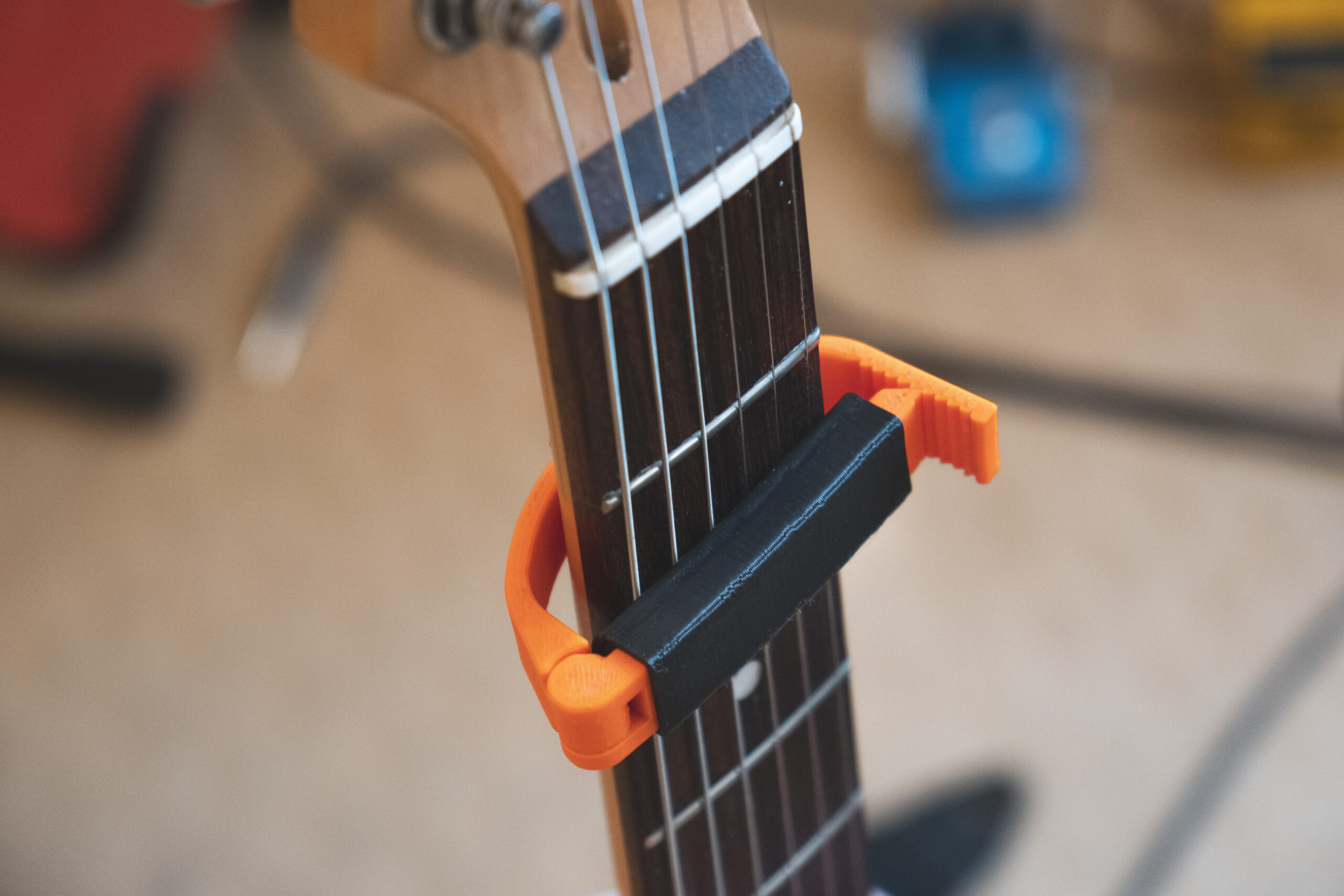
Le matériel
Avec le choix d’aller de l’avant avec le matériel de Telecaster, nous devons nous procurer toutes les pièces. En général, il y a 3 façons de procéder :
- Acheter une guitare Telecaster bon marché et la démonter pour les pièces
- Acheter toutes les pièces individuellement
- Acheter un kit matériel de Telecaster
Acheter une guitare entièrement fonctionnelle juste pour la démonter tout de suite semble être une façon tellement mauvaise et inutile de s’y prendre. Le seul cas où cela semblerait être une bonne solution serait si vous trouvez une guitare gravement endommagée, avec le matériel et le manche toujours en bon état.
L’achat de toutes les pièces individuellement est certainement une option réalisable. Vous auriez besoin de :
- Le manche de guitare avec les mécaniques
- Un micro simple bobinage seul
- Le chevalet avec un micro simple bobinage intégré
- Un plaque de contrôle de Telecaster avec un sélecteur à 3 positions et deux boutons
- La prise de sortie
Le problème est qu’acheter les composants individuellement coûtera cher. Même si vous optez pour les choix les moins chères, vous dépenserez probablement plusieurs centaines de dollars.
Préparez-vous pour le point clé de cette construction – Le Harley Benton Electric Guitar Kit T-Style ! Ce kit ne coûte que 88€ ! Et il comprend tout le matériel dont vous aurez besoin, entièrement pré-câblé avec des connecteurs simples qui s’emboîtent simplement. Il est vendu par la société allemande Musikhaus Thomann, l’un des plus grands détaillants d’instruments de musique au monde. Ce qui ajoute une coche à l’une des exigences de la liste – livraison internationale.
Il tellement bon marché et pratique que je devais le commander. Toute cette construction vient de se retrouver à un niveau de simplicité « commandez ce kit et imprimez les pièces ». Le kit Telecaster Harley Benton est livré avec un corps en bois non peint rudimentaire. Pour le prix, c’est incroyable qu’elle soit livrée avec un corps tout court. Mais je ne me sentirai pas mal de laisser ce corps derrière moi et d’en utiliser un imprimé.
La design de base
J’ai utilisé Fusion 360 pour concevoir le corps de la guitare. Le point de départ important était de placer correctement tous les trous de vis, l’interface de montage du manche et les fentes de l’électronique.
Cela a été rendu un peu plus facile par le fait que le kit comprend le corps en bois de base. En plaçant un mètre à côté du corps et en le prenant en photo d’aussi loin que possible, idéalement avec un zoom, on obtient un superbe gabarit avec seulement une petite distorsion de perspective. À l’aide de la fonction « Calibrer » de Fusion, vous pouvez définir l’échelle de l’image. Plus la distance de calibration est longue, plus l’erreur sera faible. Donc ici, j’ai défini l’ensemble des 50 cm sur le mètre comme plage de calibration.
J’ai tracé les positions de tous les trous dans un dessin 2D. À l’aide d’un pied à coulisse numérique, j’ai mesuré la distance entre les éléments et vérifié sur le dessin si j’obtiens la même valeur. Surtout avec des trous éloignés les uns des autres, la petite distorsion de perspective créera des inexactitudes. Toutes les dimensions sont évidemment importantes, mais celle sur laquelle je me suis particulièrement concentré est la position du chevalet. Le chevalet doit être parfaitement aligné avec le manche de la guitare afin que les cordes soient bien centrées sur toute sa longueur. Et deuxièmement, le chevalet doit être à la bonne distance du manche, pour que la guitare soit accordable. Plus précisément, la 12ème frette doit être exactement au milieu de la corde. C’est ce qu’on appelle l’intonation de la guitare et heureusement, le chevalet de la Telecaster a une plage de réglage assez large pour cela. Néanmoins, le chevalet doit être dans une bonne position pour que l’ajustement fonctionne, c’est donc quelque chose qui mérite d’être vérifié.
Avec les trous de montage en place, il était temps de faire preuve de créativité. Même si j’utilise du matériel d’une Telecaster, je n’avais pas l’intention de simplement copier la bonne vieille forme Telecaster. Avec l’impression 3D, toutes les formes sont possibles, il serait donc dommage de ne pas en profiter.
J’ai toujours aimé les formes de guitare Fender Jazzmaster et Mustang. J’ai donc utilisé l’outil Spline dans Fusion 360 pour créer une forme générale inspirée de ces guitares.
L’épaisseur typique d’un corps de guitare est de 45 mm, cette valeur a été utilisée pour extruder l’esquisse. J’ai ensuite extrudé tous les trous et fentes pour l’électronique en utilisant le modèle créé auparavant. Gardant à l’esprit que toute l’électronique devra être connectée ensemble, j’ai soustrait quelques cylindres du corps pour créer des « tunnels » entre les cavités. La fente de micro du bas sera recouverte par le chevalet métallique et celle du haut par un pickguard, donc les fentes peuvent être un peu plus grandes que ce qui est strictement nécessaire. Enfin, un trou plus grand sur le bord inférieur se connecte à la fente de la plaque de contrôle. La prise de sortie sera située là. Avec cela, le modèle de base de la guitare était terminé !
Bien sûr, il y a un petit problème. Le modèle est bien trop grand pour tenir sur la plupart des imprimantes 3D de bureau. Zut, il ne rentre même pas sur l’Original Prusa XL. Il était donc temps de le couper en petits morceaux.
En plus d’être trop grand, le modèle manquait encore d’élégance ou d’une touche de design amusante. L’impression 3D n’étant pas liée aux limitations de design traditionnelles, j’ai expérimenté avec l’ajout de diverses découpes. J’ai fini par, vous l’avez deviné, des hexagones ! Il y a une motivation fonctionnelle derrière ce choix. Les hexagones créeront une tonne d’arêtes, le long desquelles il sera facile de diviser le modèle en plusieurs pièces. Et la jointure sera pratiquement invisible, car elle ressemblera à une partie prévue du design. J’ai également ajouté un grand chanfrein sur tout le bord supérieur. Cela le rendra beaucoup plus confortable pour jouer et reposer le bras.
La diviser en pièces
Vous vous souvenez quand j’ai parlé des 50 kg de force que les cordes appliquent sur le manche et le corps ? Cela crée une exigence critique pour le processus de division. Si cela est possible, la section de la guitare entre le manche et le chevalet doit être faite d’une seule pièce. Il serait inutilement compliqué de rendre suffisamment solide le lien entre deux pièces dans cette section.
Heureusement, avec un peu d’imagination, cela s’est avéré possible. Le bord supérieur est défini par le motif hexagonal. Une autre coupe évidente doit être faite juste sous les trous pour le montage du chevalet. Cela permet de garder la pièce aussi courte que possible. Et une coupe intelligente en bas à gauche permet l’orientation, dans laquelle le côté le plus long du modèle s’aligne avec la diagonale du volume d’impression. Il en résulte même que cette pièce est imprimable sans support. Cependant, nous avons décidé d’utiliser les supports organiques de PrusaSlicer pour une meilleure finition sur les surfaces en surplomb.
Placer le reste des coupes est assez simple. La pièce inférieure restante sans hexagones est divisée en deux afin que chaque pièce tienne sur la plaque de construction de 25×21 cm. Et la pièce supérieure finit par être divisée en 3 sections pour la même raison.
La dernière grande pièce qui nous manque est le pickguard, qui sert également de point de montage pour le micro supérieur. Sa forme est assez bien définie par les bords environnants, qui sont simplement en retrait de 3 mm.
Avoir le corps divisé en plusieurs pièces a un avantage supplémentaire – chaque pièce peut être imprimée avec une couleur différente. Le thème des couleurs ici chez Prusa Research est assez évident, vous ne pouvez pas vous tromper avec le noir et l’orange. Une couleur supplémentaire que j’aime utiliser avec le Prusa Orange est le bleu/teal complémentaire. Donner cette couleur à la petite pièce en bas à droite donne vraiment vie au modèle.
Et avec ça, le modèle Prusacaster est terminé !
Impression et assemblage
Le choix des matériaux pour la pièce maîtresse
La seule pièce qui subira une charge mécanique importante est la grande pièce centrale. Il pourrait être tentant de l’imprimer à partir d’un matériau comme le PETG pour plus de « résistance ». Cependant, dans notre cas, nous recherchons spécifiquement une matière très rigide (module de flexion élevé). Et peut-être étonnamment, le bon vieux PLA est fantastique à cet égard. L’utilisation de PLA correspond également au thème de cette construction en la gardant bon marché et simple.
L’utilisation du PLA a un inconvénient : la faible résistance en température. La pièce maîtresse étant assez lourde, elle pourra toujours résister au soleil direct pendant des périodes de temps raisonnablement longues. Mais si l’on devait laisser la guitare dans un étui par une très chaude journée d’été, ce serait un problème. Si vous souhaitez supprimer cette limitation, choisissez un matériau rigide avec une résistance à la température plus élevée – comme le Prusament PC Blend Carbon Fiber, le Prusament PA11 Carbon Fiber, ou similaire. Ceux-ci sont un peu plus difficiles à imprimer et un peu plus chers cependant. Étant donné que Prague a principalement un climat modéré, j’ai imprimé cette pièce avec du PLA. Et après un an (c’est le temps qu’il a fallu pour terminer cet article), elle tient toujours bon.
Pour tester si tout va bien, j’ai imprimé une copie de la pièce du milieu avec les réglages par défaut de PrusaSlicer. Et comme tout allait bien, j’y ai attaché le manche de la guitare et le chevalet, puis j’ai attaché les cordes à la « guitare ». Et voilà ! La guitare est fonctionnelle ! Elle semble plutôt étrange avec juste la pièce centrale et il manque toute l’électronique. Mais elle sonne !
Flux du matériau à froid (fluage)
Il y avait cependant une autre préoccupation – le fluage du matériau. En science des matériaux, le fluage est la tendance d’un matériau solide à se déformer lentement sous l’influence d’une contrainte mécanique persistante. Même si cette contrainte est inférieure à la limite d’élasticité du matériau. Et cette inquiétude s’est avérée vraie. Après un mois avec la pièce imprimée sous la tension des cordes, la pièce était légèrement pliée. Ce n’était pas une énorme surprise, car le profil par défaut de PrusaSlicer n’utilise que 2 périmètres, ce qui est bon pour la plupart des cas d’utilisation, mais un peu trop juste pour une pièce soumise à une telle charge mécanique. La réimpression de la pièce avec 7 périmètres et 25 % de remplissage cubique a complètement résolu le problème.
Choix des cordes
Les cordes de guitare sont disponibles dans une variété de tirants (épaisseurs). Les cordes de guitare plus fines sont généralement plus faciles à jouer et permettent de tirer plus facile des notes (bends). Elles se cassent plus facilement et produisent un peu moins de volume. Les cordes de guitare épaisses, par contre, produisent plus de volume et de sustain, mais nécessitent plus de pression des doigts pour jouer et tirer les notes. Plus important, des cordes plus épaisses appliquent plus de tension au manche de la guitare ! En sélectionnant des cordes très fines, telles que le tirant 9, nous pouvons réduire la contrainte appliquée à la pièce centrale.
Impression du reste des pièces
Le reste des pièces ne sera pas vraiment soumis à des contraintes importantes, à part tenir la guitare sur une sangle ou devoir tenir le câble. Donc, le choix du matériau ici n’a pas vraiment d’importance. J’ai imprimé les 3 premières pièces hexagonales en Prusament PETG Prusa Orange, la pièce inférieure qui maintient les interrupteurs en Prusament PLA Galaxy Black, et enfin le petit morceau en bas en Prusament PLA Azure Blue. J’ai utilisé les profils par défaut pour toutes ces pièces.
Connexion des pièces
Toutes les pièces ont de grandes surfaces de contact avec la pièce centrale. Utilisez une quantité généreuse de superglue pour coller le tout ensemble. Il y a des trous de vis M3 dans les pièces hexagonales pour renforcer la connexion, car toute la guitare sera accrochée à ceux-ci si vous utilisez une sangle.
Câblage de l’électronique
Les câbles du kit Harley Benton T-style sont tous livrés avec des connecteurs JST, il est donc très facile de tout connecter ensemble. Assurez-vous simplement de connecter les câbles du micro supérieur aux câbles provenant du haut du sélecteur. Sinon, le commutateur fonctionnerait dans le sens inverse – la position du haut sélectionnerait le micro du bas.
Une chose intéressante à propos du câblage est le fil noir tout seul qui ne se connecte apparemment à rien. Il est utilisé pour mettre les cordes à la terre. Vous trouverez un canal dans la pièce imprimée centrale qui passe sous le chevalet. Dénudez un peu l’isolant du câble, desserrez un peu le chevalet, faites passer le câble noir à travers celui-ci et sertissez-le en resserrant à nouveau le pont. Sans cette mise à la terre, la guitare bourdonnerait beaucoup. Même sur des guitares assez chères, il y aura toujours du bourdonnement (et nous utilisons des composants pas chers), mais cela aidera considérablement à l’atténuer.
Réglage final – réglage de l’intonation de la guitare
Avec la guitare entièrement assemblée, vous pouvez mettre les cordes sur la guitare et l’accorder. Après avoir accordé les cordes, vous pouvez régler l’intonation de la guitare, afin qu’elle soit parfaitement accordée sur toute la touche. Une fois les cordes accordées, jouez la même corde à vide et à la 12ème frette. Si la note à la 12ème frette est désaccordée (plus que légèrement) par rapport à la note ouverte, vous devrez ajuster l’intonation. Sur le matériel Telecaster, c’est en fait extrêmement facile à faire. Vous pouvez déplacer la partie du chevalet qui pousse les cordes vers le haut (c’est ce qu’on appelle le sillet), en tournant la vis qui la traverse. Si la note frettée est plate (plus grave), déplacez le sillet vers le manche. Si la note frettée est aiguë (plus haute en intonation), détendez d’abord légèrement la corder puis déplacez le sillet vers le chevalet. Gardez à l’esprit que les curseurs du sillet d’une Telecaster sont partagés par deux cordes, alors essayez de trouver un bon compromis où les deux cordes sont accordées.
La guitare entièrement assemblée
Comment sonne-t-elle ?
La guitare sonne vraiment étonnamment bien. Si j’avais les yeux fermés et que quelqu’un me la tendait, je ne pourrais peut-être même pas dire qu’elle est imprimée en 3D. Les cordes restent bien accordées et l’intonation de la guitare est presque parfaite. Bien sûr, comme les composants étaient assez bon marché, on ne peut pas s’attendre à ce qu’elle sonne mieux qu’une Telecaster haut de gamme, mais pour le prix, c’est un excellent résultat.
Téléchargez le design et créez la vôtre !
Dans l’ensemble, je suis extrêmement satisfait du résultat. Si vous souhaitez créer votre propre Prusacaster, vous pouvez télécharger le modèle 3D sur Printables.com.
Téléchargez le modèle sur Printables.com
Comme toujours, c’est un téléchargement gratuit, alors allez-y et essayez-la ! J’espère que vous aurez autant de plaisir à construire votre propre Prusacaster que moi.
Bonjour,
Magnifique projet. Je me lance dans l'aventure🤞
Superbe projet mais : après 3 mois le manche cherche à se séparer du body et les cordes s'éloignent tranquillement du manche. Il y a trop de tension pour du plastique d'après moi… J'ai plusieurs guitares haut de gamme et je voulais essayer ce projet cool, mais malheureusement je ne pourrai jamais faire un show avec, elle est beaucoup trop instable.