Eine E-Gitarre in 3D zu drucken war schon immer ein Traum von mir, aber es schien mir eine entmutigende Aufgabe zu sein. Würde der Korpus unter der Spannung der Saiten brechen? Würde er sich mit der Zeit verbiegen? Würde ich spezielle aktive Tonabnehmer verwenden müssen? Würde der Kunststoffkorpus im Vergleich zu traditionellem Hartholz einen schrecklichen Klang erzeugen? Es gab so viele Fragen und überraschend wenige Antworten, die man online finden konnte.
Ich bin natürlich nicht der erste, der dies versucht. Es gibt mehrere Artikel und Modelle, die online verfügbar sind, und einige der Designs sind sehr gut gelungen. Allerdings waren viele dieser gedruckten Gitarren nicht wirklich spielbar, und einige Projekte, die gut aussahen, hatten entweder das 3D-Modell nicht dabei, es fehlte eine Anleitung, sie waren zu kompliziert oder zu teuer.
Und so wurde es beschlossen – Ich werde meine eigene 3D-druckbare E-Gitarre von Grund auf entwerfen.
Entwurfsprioritäten
Um den Gedankenprozess zu verstehen – ich habe die Gitarre mit Blick auf die 3D-Druck-Community entworfen. Ich möchte, dass andere diesen Bau leicht nachvollziehen und ihre eigene fantastische Gitarre erstellen können. Bevor ich also mit dem Design begann, habe ich eine Liste mit Prioritäten aufgestellt:
- Das Projekt sollte einfach sein
- Keine komplizierten Baugruppen aus Dutzenden von Teilen, einfach zusammenzubauen
- Keine Metallstangen zur Verstärkung oder andere unwichtige Hardware
- Sie sollte billig sein, wenn ich eine Menge Geld für eine Gitarre ausgebe, kaufe ich eine echte Fender oder Gibson
- Die Hardware sollte einfach zu beschaffen sein mit weltweitem Versand
- Alle Teile müssen auf den Original Prusa i3 MK3S+ (25×21×21 cm) passen
- Das scheint eine wirklich harte Einschränkung zu sein, aber wenn es nicht auf einem Drucker der Größe MK3 gedruckt werden kann, werden die meisten Leute nicht in der Lage sein, es zu drucken
- Sie sollte sich tatsächlich gut spielen lassen und über die gesamte Bandbreite hinweg stimmig sein, ich möchte kein unspielbares Kunststoff-Gimmick erschaffen
- Sie sollte unglaublich cool aussehen!
Keeping it simple
Die größte Sorge war von Anfang an die Kraft, die die Saiten auf den Korpus und den Hals der Gitarre ausüben. Die Quellen unterscheiden sich zwar leicht in den Angaben dazu, aber der Konsens scheint zu sein, dass es sich um etwa 50 kg Belastung handelt, je nach Saitenstärke (Dicke). Diese 50 kg versuchen, die Gitarre in der Hälfte zu falten, den Steg aus dem Korpus zu reißen und den Hals stark zu verbiegen.
Das Problem des Halses zu lösen, war eine ganz einfache Entscheidung – ich werde einen echten Holzhals verwenden. Man könnte zwar argumentieren, dass die Gitarre nicht mehr „vollständig 3d-gedruckt“ sein wird, aber der Hals ist ein so wichtiger und empfindlicher Teil des Instruments, dass es das gesamte Projekt gefährden würde, wenn ich ihn drucken wollte (auch wenn es möglich ist). Hölzerne Hälse sind vollkommen glatt und gerade, haben verschleißfeste Metallbünde und verfügen über eine Stange im Inneren, mit der das Relief (konkaver oder konvexer Bogen) eingestellt werden kann.
Die Lösung des Brückenproblems erforderte jedoch mehr Nachdenken. Der Steg einer E-Gitarre ist ein kleines Metallteil, das das untere Ende der Saiten hält. Er ist normalerweise mit ein paar Schrauben am Korpus befestigt. Wenn wir uns die gängigsten Gitarrendesigns ansehen, könnte Ihnen eine der Brücken als besonders geeignet für eine 3D gedruckte Gitarre auffallen. Können Sie erraten, welche es ist?
Bis auf eine Ausnahme haben alle gängigen Gitarrendesigns einen sehr kleinen Steg, der manchmal nur mit 2 Schrauben befestigt wird. Die Brücke der Telecaster ist jedoch eine ganz andere Geschichte! Diese große Metallplatte hält nicht nur die unteren Saiten an ihrem Platz, sondern integriert auch den unteren Tonabnehmer und verfügt über bis zu 5 Befestigungslöcher mit weit auseinander liegenden Schraubenlöchern, die eine bessere Verteilung der Hebelwirkung auf die Brücke über die gesamte Metallplatte und das darunter liegende gedruckte Teil ermöglichen.
Außerdem hat die Telecaster nur einen zusätzlichen Tonabnehmer, was die Verkabelung und das Design vereinfacht. Und schließlich sind die Lautstärke- und Stimmknöpfe sowie der Tonabnehmer-Wahlschalter alle auf einer anderen Metallplatte montiert und mit nur 2 Schrauben am Korpus befestigt. Das vereinfacht das Projekt enorm, da wir nicht mehrere Knöpfe und Schalter einzeln in die Gitarre integrieren müssen.
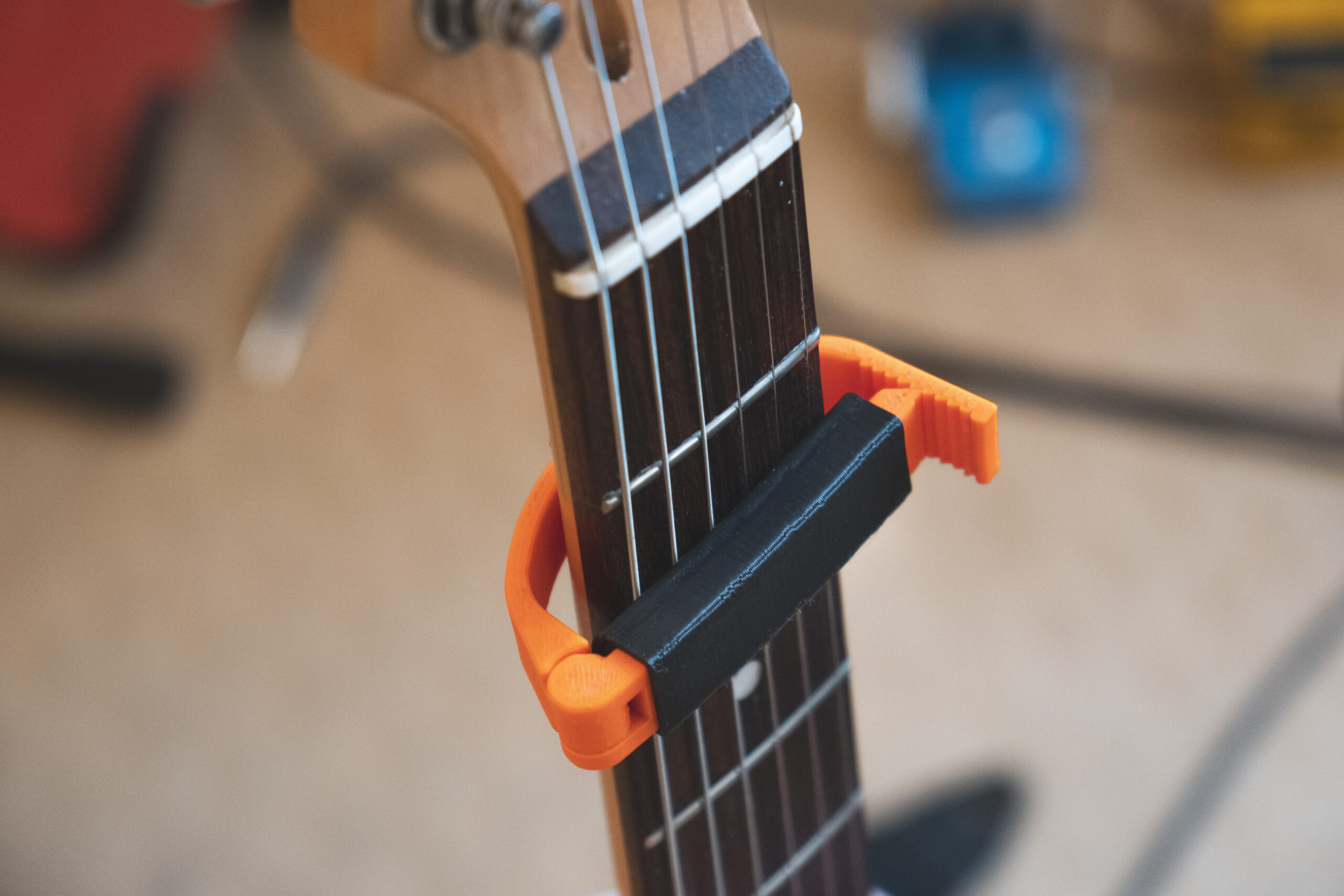
Die Hardware
Da die Entscheidung für die Telecaster-Hardware gefallen ist, müssen wir alle Teile beschaffen. Im Allgemeinen gibt es 3 Möglichkeiten, dies zu tun:
- Kaufen Sie eine billige Telecaster-Gitarre und zerlegen Sie sie für die Teile
- Kaufen Sie alle Teile einzeln
- Kaufen Sie einen Telecaster-Bausatz
Eine ganze funktionstüchtige Gitarre zu kaufen, nur um sie gleich wieder zu zerlegen, scheint mir ein falscher und verschwenderischer Weg zu sein. Das einzige Mal, dass dies eine gute Lösung zu sein scheint, wäre, wenn Sie eine stark beschädigte Gitarre finden, bei der die Hardware und der Hals noch in einem guten Zustand sind.
Alle Teile einzeln zu kaufen, ist definitiv eine machbare Option. Sie bräuchten:
- Den Gitarrenhals mit Stimmgeräten
- 1 eigenständiger Single-Coil Tonabnehmer
- Die Brücke mit integriertem Single-Coil-Tonabnehmer
- Telecaster-Kontrollplatte mit einem 3-Wege-Schalter und zwei Knöpfen
- Die Ausgangsbuchse
Das Problem ist, dass der Einzelkauf der Komponenten teuer wird. Selbst wenn Sie sich für die absolut billigsten Optionen entscheiden, werden Sie wahrscheinlich mehrere hundert Dollar ausgeben.
Bereiten Sie sich auf den Knaller dieses Bausatzes vor – Das Harley Benton Electric Guitar Kit T-Style! Dieser Bausatz kostet nur $79! Und es enthält die gesamte Hardware, die Sie benötigen, alles vorverkabelt mit einfachen Steckern, die einfach zusammenschnappen. Es wird vom deutschen Musikhaus Thomann verkauft, einem der größten Musikinstrumentenhändler der Welt. Damit ist eine der Anforderungen auf der Liste abgehakt – weltweiter Versand.
Es ist so günstig und praktisch, dass ich es einfach bestellen musste. Dieser ganze Bau wurde zu einem einfachen „Bestelle diesen Bausatz und drucke die Teile“ Level. Der Harley Benton Telecaster-Bausatz wird mit einem rudimentären unlackierten Holzkorpus geliefert. Für den Preis ist es erstaunlich, dass er überhaupt mit einem Korpus geliefert wird. Aber ich hätte kein schlechtes Gewissen, diesen Korpus zurückzulassen und einen gedruckten zu verwenden.
Das Grunddesign
Ich habe Fusion 360 verwendet, um den Korpus der Gitarre zu entwerfen. Der wichtigste Ausgangspunkt war, alle Schraubenlöcher, die Schnittstelle für die Halsbefestigung und die Steckplätze für die Elektronik richtig zu platzieren.
Dies wurde durch die Tatsache, dass der Bausatz einen Holzkorpus enthält, erheblich erleichtert. Indem wir ein Metermaß neben das Gehäuse legen und es aus größtmöglicher Entfernung fotografieren, idealerweise mit einem Zoomobjektiv, erhalten wir eine großartige Vorlage mit nur geringer perspektivischer Verzerrung. Mit der Funktion „Kalibrieren“ von Fusion können Sie den Maßstab des Bildes einstellen. Je länger die Kalibrierungsdistanz ist, desto geringer ist der Fehler. Hier habe ich also die gesamten 50 cm auf dem Metermaß als meinen Kalibrierungsbereich eingestellt.
Ich habe die Positionen aller Löcher in einer 2D-Zeichnung nachgezeichnet. Mit einem digitalen Messschieber habe ich den Abstand zwischen den Merkmalen gemessen und in der Zeichnung überprüft, ob ich den gleichen Wert erhalte. Besonders bei Löchern, die weit auseinander liegen, führt die kleine perspektivische Verzerrung zu einigen Ungenauigkeiten. Alle Maße sind natürlich wichtig, aber das, worauf ich mich besonders konzentriert habe, ist die Position der Brücke. Der Steg muss perfekt auf den Hals der Gitarre ausgerichtet sein, damit die Saiten über die gesamte Länge schön zentriert sind. Und zweitens muss der Steg den richtigen Abstand zum Hals haben, damit die Gitarre stimmbar ist. Insbesondere sollte der 12. Bund genau in der Mitte der Saite liegen. Dies wird als Intonation der Gitarre bezeichnet, und glücklicherweise hat der Telecaster-Steg dafür einen ziemlich großen Einstellbereich. Dennoch muss der Steg in einer guten Position sein, damit die Einstellung funktioniert. Es lohnt sich also, dies zweimal zu überprüfen.
Nachdem die Befestigungslöcher angebracht waren, war es an der Zeit, kreativ zu werden. Obwohl ich Telecaster-Hardware verwende, hatte ich nicht vor, einfach die gute alte Telecaster-Form zu kopieren. Mit dem 3D-Druck ist jede Form möglich, und es wäre eine Schande, dies nicht auszunutzen.
Ich mochte schon immer die Formen der Fender Jazzmaster und Mustang Gitarren. Also habe ich das Spline-Werkzeug in Fusion 360 verwendet, um eine allgemeine Form zu erstellen, die von diesen Gitarren inspiriert ist.
Die typische Dicke eines Gitarrenkorpus beträgt 45 mm, dieser Wert wurde zum Extrudieren der Skizze verwendet. Dann habe ich alle Löcher und Schlitze für die Elektronik extrudiert, indem ich die zuvor erstellte Vorlage verwendet habe. Da die gesamte Elektronik miteinander verbunden werden muss, habe ich ein paar Zylinder vom Korpus abgezogen, um „Tunnel“ zwischen den Hohlräumen zu schaffen. Der untere Tonabnehmerschlitz wird von der Metallbrücke und der obere von einem Schlagbrett verdeckt, so dass die Schlitze etwas größer sein können als unbedingt nötig. Ein größeres Loch am unteren Rand verbindet sich mit dem Schlitz für die Steuerplatte. Dort wird die Ausgangsbuchse untergebracht sein. Damit war das Grundmodell der Gitarre fertig!
Natürlich gibt es ein kleines Problem. Das Modell ist viel zu groß, um auf die meisten Desktop-3D-Drucker zu passen. Zum Teufel, es passt nicht einmal auf den Original Prusa XL. Es war also an der Zeit, es in kleinere Stücke zu schneiden.
Abgesehen davon, dass es zu groß war, fehlte dem Modell noch etwas Eleganz oder eine witzige Designvariante. Da der 3D-Druck nicht an die traditionellen Designbeschränkungen gebunden ist, habe ich mit verschiedenen Ausschnitten experimentiert. Am Ende hatte ich, Sie ahnen es, Sechsecke! Diese Wahl hat einen funktionalen Grund. Die Sechsecke erzeugen eine Menge Kanten, entlang derer es einfach ist, das Modell in mehrere Teile zu zerlegen. Und die Naht wird im Grunde genommen unsichtbar sein, da sie wie der beabsichtigte Teil des Designs aussehen wird. Ich habe auch eine große Fase entlang der gesamten Oberkante hinzugefügt. Das macht das Spielen und das Abstützen des Arms viel bequemer.
Aufteilung in Teile
Erinnern Sie sich, als ich über die 50 kg Kraft sprach, die die Saiten auf den Hals und den Korpus ausüben? Daraus ergibt sich eine entscheidende Voraussetzung für den Aufteilungsvorgang. Wenn irgend möglich, sollte der Teil der Gitarre zwischen Hals und Steg aus einem einzigen Stück gemacht werden. Es wäre unnötig kompliziert, die Verbindung zwischen zwei Teilen in diesem Abschnitt stark genug zu machen.
Glücklicherweise war dies mit etwas Phantasie möglich. Die obere Kante wird durch das Sechseckmuster definiert. Ein weiterer offensichtlicher Schnitt muss direkt unter den Löchern für die Befestigung der Brücke gemacht werden. So bleibt das Teil so kurz wie möglich. Und ein cleverer Schnitt unten links ermöglicht eine Ausrichtung, bei der die längste Seite des Modells mit der Diagonale des Druckvolumens übereinstimmt. Das führt sogar dazu, dass dieses Teil ohne Stützen druckbar ist. Wir haben uns jedoch entschieden, die organischen Stützen von PrusaSlicer zu verwenden, um die überhängenden Flächen schöner zu gestalten.
Das Anbringen der restlichen Teile ist ziemlich einfach. Das übrig gebliebene Unterteil ohne Sechsecke wird in zwei Teile geteilt, damit jedes Teil auf die 25×21 cm große Bauplatte passt. Und das Oberteil wird aus demselben Grund in 3 Teile geteilt.
Das letzte große Teil, das uns fehlt, ist das Schlagbrett, das auch als Befestigungspunkt für den oberen Tonabnehmer dient. Seine Form ist durch die umliegenden Kanten, die einfach um 3 mm eingefügt sind, ziemlich gut definiert.
Die Aufteilung des Korpus in mehrere Teile hat einen weiteren Vorteil – jedes Teil kann mit einer anderen Farbe gedruckt werden. Das Farbthema hier bei Prusa Research ist ziemlich offensichtlich, mit Schwarz und Orange kann man nichts falsch machen. Eine zusätzliche Farbe, die ich gerne mit dem Prusa Orange verwende, ist das komplementäre Blau/Grün. Wenn Sie das kleine Stück unten rechts mit dieser Farbe einfärben, wird das Modell wirklich lebendig.
Und damit ist das Prusacaster-Modell fertig!
Drucken und Zusammenbau
Die Materialwahl für das Mittelstück
Das einzige Teil, das einer erheblichen mechanischen Belastung ausgesetzt sein wird, ist das große Mittelstück. Es mag verlockend sein, es aus einem Material wie PETG zu drucken, um es „stabiler“ zu machen. Aber in unserem Fall suchen wir speziell nach einem sehr steifen Material (hoher Biegemodul). Und vielleicht ist es überraschend, dass das gute alte PLA in dieser Hinsicht fantastisch ist. Die Verwendung von PLA passt auch zum Thema dieses Baus, der billig und einfach sein soll.
Die Verwendung von PLA hat einen Nachteil – die Beständigkeit bei niedrigen Temperaturen. Da das Mittelstück recht schwer ist, kann es der direkten Sonne noch einigermaßen lange standhalten. Aber wenn man die Gitarre an einem sehr heißen Sommertag in einem Koffer liegen lässt, wäre das ein Problem. Wenn Sie diese Einschränkung beseitigen wollen, wählen Sie ein steifes Material mit höherer Temperaturbeständigkeit – wie Prusament PC Blend Carbon Fiber, Prusament PA11 Carbon Fiber, oder ähnliches. Diese sind allerdings etwas schwieriger zu drucken und auch ein wenig teurer. Da in Prag meist ein gemäßigtes Klima herrscht, habe ich dieses Teil aus PLA gedruckt. Und nach einem Jahr (so lange hat die Fertigstellung dieses Artikels gedauert) hält es immer noch gut.
Um zu testen, ob alles passt, habe ich ein Exemplar des mittleren Teils mit den Standardeinstellungen des PrusaSlicer gedruckt. Und da alles passte, habe ich den Gitarrenhals und die Brücke daran befestigt und dann die Saiten an der „Gitarre“ angebracht. Und Voilà! Die Gitarre ist funktionsfähig! Sie sieht etwas seltsam aus, nur mit dem Mittelstück, und es fehlt die gesamte Elektronik. Aber sie spielt!
Kaltfließen des Materials (Kriechen)
Es gab jedoch noch eine weitere Sorge – das Kriechen von Materialien. In der Materialwissenschaft bezeichnet Kriechen die Tendenz eines festen Materials, sich unter dem Einfluss einer anhaltenden mechanischen Spannung langsam zu verformen. Selbst wenn diese Spannung unterhalb der Streckgrenze des Materials liegt. Und diese Befürchtung erwies sich als wahr. Nach einem Monat, in dem das gedruckte Teil unter der Spannung von Saiten stand, war das Teil leicht verbogen. Das war keine große Überraschung, denn das Standardprofil in PrusaSlicer verwendet nur 2 Perimeter, was für die meisten Anwendungsfälle gut ist, aber ein bisschen zu wenig für ein Teil, das einer solchen mechanischen Belastung ausgesetzt ist. Wenn Sie das Teil mit 7 Perimetern und 25% kubischem Infill neu drucken, ist das Problem vollständig gelöst.
Auswahl der Saiten
Gitarrensaiten gibt es in verschiedenen Stärken (Gauges). Leichtere Gitarrensaiten sind in der Regel einfacher zu spielen und ermöglichen ein leichteres Biegen der Noten. Sie reißen allerdings auch leichter und erzeugen etwas weniger Lautstärke. Schwere Gitarrensaiten hingegen erzeugen mehr Volumen und Sustain, erfordern aber mehr Fingerdruck zum Spielen und Biegen von Noten. Noch wichtiger ist, dass schwerere Saiten mehr Spannung auf den Gitarrenhals ausüben! Durch die Wahl sehr dünner Saiten, wie z.B. 9 Gauge, können wir die auf das Mittelstück wirkende Spannung verringern.
Drucken der restlichen Teile
Der Rest der Teile wird nicht wirklich einer nennenswerten Belastung ausgesetzt sein, abgesehen davon, dass sie die Gitarre an einem Gurt halten oder das Kabel halten müssen. Die Wahl des Materials ist hier also nicht wirklich wichtig. Ich habe die oberen 3 sechseckigen Teile aus Prusament PETG Prusa Orange gedruckt, das untere Teil, das die Schalter hält, aus Prusament PLA Galaxy Black, und schließlich das kleine Teil unten aus Prusament PLA Azure Blue. Ich habe für alle diese Teile die Standardprofile verwendet.
Verbinden der Teile
Alle Teile haben große Kontaktflächen mit dem Mittelstück. Verwenden Sie eine großzügige Menge Sekundenkleber, um alles zusammenzukleben. In den Sechskantteilen befinden sich M3-Schraubenlöcher, um die Verbindung zu verstärken, da die ganze Gitarre daran hängen wird, wenn Sie einen Gurt verwenden.
Verkabelung der Elektronik
Die Kabel im Harley Benton T-Style Kit sind alle mit JST-Steckern versehen, so dass es wirklich einfach ist, alles miteinander zu verbinden. Stellen Sie nur sicher, dass Sie die Kabel vom oberen Tonabnehmer mit den Kabeln verbinden, die von der Oberseite des Umschalters kommen. Andernfalls würde der Schalter in umgekehrter Weise funktionieren – die obere Position würde den unteren Tonabnehmer auswählen.
Eine interessante Sache an der Verkabelung ist das einzelne schwarze Kabel, das scheinbar mit nichts verbunden ist. Es dient dazu, die Saiten zu erden. In der Mitte des gedruckten Teils finden Sie einen Kanal, der unter die Brücke führt. Isolieren Sie das Kabel ab, lockern Sie den Steg ein wenig, führen Sie das schwarze Kabel hindurch und klemmen Sie es ein, indem Sie den Steg wieder festziehen. Ohne diese Erdung würde die Gitarre unangenehm viel brummen. Selbst bei recht teuren Gitarren wird es immer ein gewisses Brummen geben (und wir verwenden preisgünstige Komponenten), aber dies wird erheblich dazu beitragen, das Brummen zu vermindern.
Abschließende Einstellung – Intonation der Gitarre
Wenn die Gitarre vollständig zusammengebaut ist, können Sie die Saiten aufziehen und die Gitarre stimmen. Nachdem Sie die Saiten gestimmt haben, können Sie die Intonation der Gitarre einstellen, so dass sie über das gesamte Griffbrett perfekt gestimmt ist. Sobald die Saiten gestimmt sind, spielen Sie dieselbe Saite sowohl offen als auch am 12. Wenn die Note am 12. Bund im Vergleich zur offenen Note mehr als nur leicht verstimmt ist, müssen Sie die Intonation korrigieren. Bei der Telecaster-Hardware ist das eigentlich sehr einfach. Sie können den Teil des Stegs, der die Saiten nach oben drückt (er wird Sattel genannt), durch Drehen der Schraube, die durch ihn hindurchgeht, verschieben. Wenn die gespielte Note flach ist (tiefer in der Tonhöhe), bewegen Sie den Sattel in Richtung des Halses. Wenn die gegriffene Note scharf ist (höher in der Tonhöhe), lockern Sie zuerst die Saite etwas und bewegen Sie dann den Sattel in Richtung Steg. Denken Sie daran, dass sich die Sattelschieber bei einer Telecaster zwei Saiten teilen, versuchen Sie also, einen guten Mittelweg zu finden, bei dem beide Saiten gestimmt sind.
Die komplett montierte Gitarre
Wie spielt sie sich?
Die Gitarre spielt wirklich erstaunlich gut. Wenn ich die Augen schließe und jemand sie mir in die Hand drückt, würde ich vielleicht gar nicht merken, dass sie in 3D gedruckt ist. Die Saiten bleiben gut gestimmt, und die Intonation der Gitarre ist nahezu perfekt. Da die Komponenten recht billig waren, kann man natürlich nicht erwarten, dass sie besser spielt als eine High-End-Telecaster, aber für den Preis ist das ein tolles Ergebnis.
Laden Sie das Design herunter und machen Sie Ihr eigenes!
Insgesamt bin ich mit dem Ergebnis der Gitarre sehr zufrieden. Wenn Sie Ihren eigenen Prusacaster machen möchten, können Sie das 3D-Modell bei Printables.com herunterladen.
Downloaden Sie das Modell von Printables.com
Wie immer ist der Download kostenlos, also probieren Sie es einfach aus! Ich hoffe, Sie werden genauso viel Spaß beim Bau Ihres eigenen Prusacasters haben wie ich.
Super, werd ich wahrscheinlich nachbauen
Hilfreich wäre eine Liste der gedruckten Teile mit Angabe der druckparameter
Schöne Arbeit! Jetzt auch noch gleich einen E-Bass umsetzten, gibt es ja auch als Teilebausatz von https://www.thomann.de/de/harley_benton_bass_guitar_kit_j_style.htm
Hallo Vielen Dank für diese wunderschöne Gitarre. Ich habe Sie gedruckt, allerdings habe ich ein Problem mit dem Bausatz der Gitarre von Thomann. der Tonabnehmer mit der Einstellplatte ist in der Einbauhöhe 6 mm größer als der angegebene. Jetzt habe ich mir gedacht das Teil black core entsprechend anzupassen, allerdings finde ich gerade diese Datei nicht um sie in Fusion 360 zu bearbeiten. Sie ist nur als stl Datei vorhanden. Könnten Sie mir diese Datei noch als STEP Datei zur Verfügung stellen. Vielen Dank im Voraus Günther Merz