Formula racing combines thrill and action. In this highly competitive world, the smallest details determine the line between success and failure. Elite engineers push the limits of technology and try to outwit each other, while the drivers attempt to navigate the car just perfectly, often risking everything. Today, we’d like to offer you a look behind the curtain — what AIX Racing team does to be competitive and how they use Original Prusa 3D printers to succeed in FIA Formula championships.
AIX Racing and Prusa Research have collaborated extensively for the past few years. Our 3D printers and materials were tested to the limit — and stood up to the expectations. Today, we can safely say that 3D printing makes a huge difference, even at the premier level of motorsport. The team’s chief engineer, Arthur Rencker, says:
“3D printing makes everything easier for us,” says Arthur. And he immediately names the biggest advantages of this technology: it’s fast, on-the-spot precise, and independent of additional suppliers.
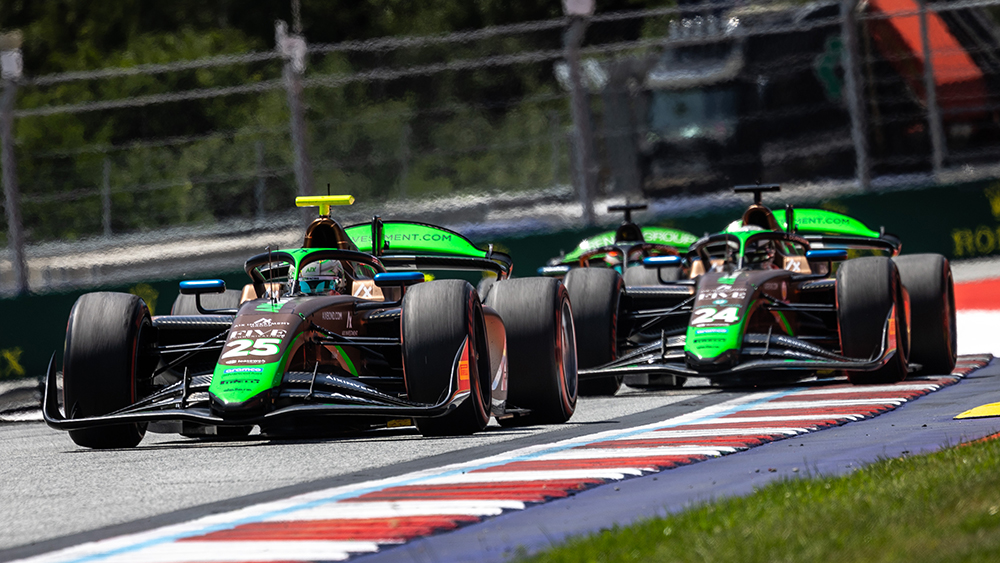
Spielberg (AUT) JUN 27-JUN 2024 – F1 Austrian GP at the Red Bull Ring. Taylor BARNARD #25 AIX Racing F2 © 2024 Dutch Photo Agency
3D printing also saves time, which the team usually doesn’t have much of. Formula racing is about speed both on the track and in the garage. There are 14 F2 races annually, and with the highly restricted testing opportunities and stringent car enhancement rules, teams have very limited time to adjust during the season. Pre-season testing is limited to about six days, spread across two to three official test sessions. In-season testing is almost non-existent, with no private tests allowed and only a few official test days available.
Also, all teams have the same cars and engines in Formula 2, Formula 3, and Formula 4. What makes the difference is the driver’s skill and the engineers who fine-tune the machines to squeeze a little extra performance out of them. And, as you might suspect, here comes 3D printing.
Custom tools and parts
3D printing is ever-present in the team’s workshop – from functional parts and various prototypes to clever tools and jigs. For example, Arthur showed us a 3D-printed custom screwdriver — with a different-sized bolt on each side and tailored fit to the hand of a specific mechanic. On the race track, a clever detail like that can save you a precious second or two.
Another necessary tool is a powerful cooler, which mechanics use to cool the engine down between laps or sessions. The cooler is a piece of hardware you can normally buy yourself, but it is enhanced with 3D printing: in particular, a mounting part that fits directly to the car engine’s intake or custom-designed battery holders that can hold more powerful cells.
Other 3D-printed parts can be found under the hood, for example, uniquely shaped airflow tubes that guide the cool air to whichever part of the car or the engine is needed. This allows the team to react to any conditions during the race. Arthur says that doing this without 3D printing would be very complicated.
The part of the car around the driver is called a “safety zone”, and the rules dictate that everything installed there must be made of self-extinguishing material. Therefore, 3D-printed accessories are printed from Prusament V0. Like this connector holder in the cockpit, which… Does something that Arthur doesn’t want anyone to know. 🙂
That brings us to an important note: If you’re wondering why you haven’t spotted any of these 3D-printed parts on TV or in press releases, the explanation is simple: Most parts or enhancements are covered with tape imitating polished carbon fiber texture. Teams do this to protect their know-how from others!
Precise prototyping saves time
The team has several Original Prusa MK4 3D printers for parts production and an Original Prusa XL that is used mostly for prototyping. The main reason for using in-house 3D printers is better control over time and resources. During the prototyping process, they make many iterations of their ideas before they make the final part using another technology.
“We print the parts, try them, tune, adjust — and only when everything works perfectly, then we CNC them from aluminum,” explains Arthur.
Often, they need to combine several large parts that must fit together perfectly, leaving no room for inaccuracy.
And that’s where 3D printing saves them the most valuable part of their busy schedule.
“Thanks to precise prototyping using 3D printing, we gain extra time we can spend on the CNC or the car,” says Arthur. There’s always something to fix or tune,” he smiles.
They also employ an SLA 3D printer — the Original Prusa SL1S — to prototype small and very detailed parts, such as gearbox wheels or other important components. For example, Arthur shows us a custom-made connector end cap. Other printed models are either various prototypes or flexible parts that complement them.
PC-Blend Carbon Fiber quickly became their go-to material because of its heat resistance, durability, and stability. With the Original Prusa Enclosure, printing from these advanced materials is easy. For simple prototypes, they use Prusament PETG. As for resins, they use Prusament Resin Tough for most models and Flex for joints and moving parts.
Workshop full of Original Prusa printers
Arthur first started 3D printing at the university. He wanted to optimize the shape and weight of a car – to make it perform better. Unlike most makers, he first tried metal 3D printing and then moved to thermoplastics – Prusament filaments in particular.
After very encouraging testing results, they started with one Original Prusa MK3 and acquired another two to keep up with production. Arthur has found more and more use cases for 3D printing, so they have now upgraded to MK4 and acquired the Original Prusa XL and the Original Prusa SL1S.
Arthur fell in love with the Original Prusa MK4 immediately. “The printer does everything by itself. I especially like the automated first-layer calibration,” he says. “The setup is easy, and it makes the whole workflow much easier,” adds Arthur.
The large built volume of the Original Prusa XL opened new possibilities for him. He started pushing the limits, and now he makes advanced prototypes of several important car parts.
“I like the XL very much. It’s as fast and reliable as the MK4, but just bigger,” smiles Arthur.
And one toolhead is not going to be enough. He reveals his plans: “We started with one toolhead, but now I decided to order a second one to make complex models with soluble supports.”
The team also takes a 3D printer with them to the race track – an Original Prusa MK3S+ in an enclosure travels with AIX Racing around the world. Every race there’s a part, component, or adjustment that needs to be 3D printed. 🙂
According to Arthur, the future of 3D printing in formula racing is more than bright.
“It’s just a matter of time before all the F2 teams have a 3D printer,“ he says.
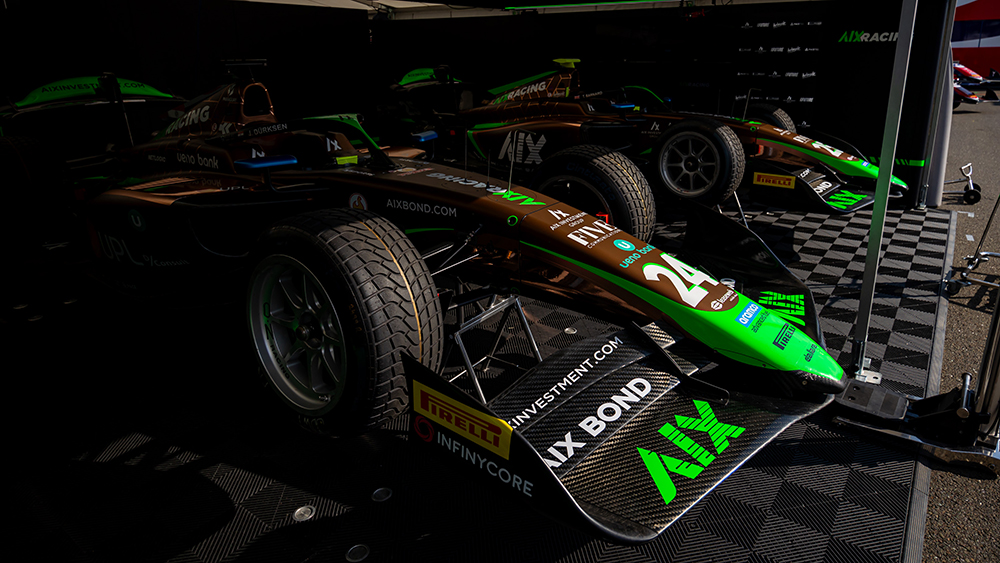
Spielberg (AUT), JUL 27-30 2024 – Austrian Grand Prix at the Red Bull Ring. AIX Racing F2. © 2024 Dutch Photo Agency
Jakub Kmošek, Jakub Fiedler and Štepán Feik
You must be logged in to post a comment.