Les courses de Formule combinent sensations fortes et action. Dans ce monde hautement compétitif, les moindres détails déterminent la frontière entre le succès et l’échec. Les ingénieurs d’élite repoussent les limites de la technologie et tentent de se déjouer les uns les autres, tandis que les pilotes tentent de conduire la voiture à la perfection, en risquant souvent tout. Aujourd’hui, nous aimerions vous offrir un aperçu de ce qui se passe derrière le rideau – ce que fait l’équipe AIX Racing pour être compétitive et comment elle utilise les imprimantes 3D Original Prusa pour réussir dans les championnats de Formule FIA.
AIX Racing et Prusa Research ont étroitement collaboré ces dernières années. Nos imprimantes 3D et matériaux ont été testés jusqu’aux limites et ont répondu aux attentes. Aujourd’hui, nous pouvons affirmer avec certitude que l’impression 3D fait une énorme différence, même au plus haut niveau du sport automobile. L’ingénieur en chef de l’équipe,Arthur Rencker, déclare :
« L’impression 3D nous facilite tout », déclare Arthur. Et il cite immédiatement les principaux avantages de cette technologie : elle est rapide, précise sur place et indépendante de fournisseurs supplémentaires.
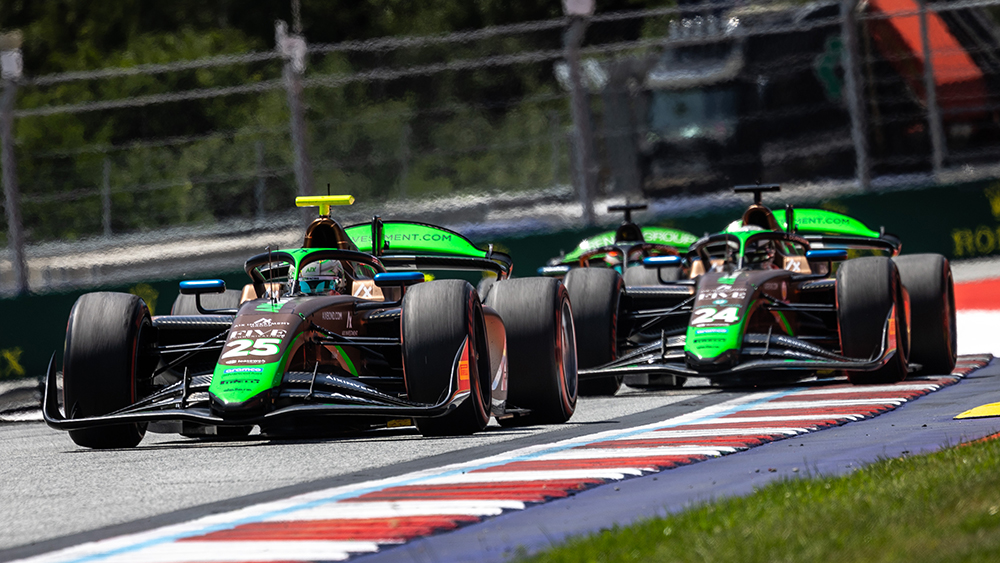
Spielberg (AUT) 27-30 juin 2024 – GP de F1 d’Autriche au Red Bull Ring. Taylor BARNARD #25 AIX Racing F2 © 2024 Dutch Photo Agency
L’impression 3D permet également de gagner du temps, dont l’équipe ne dispose généralement pas beaucoup. Les courses de Formule sont une question de vitesse, tant sur la piste que dans le garage. Il y a 14 courses de F2 par an, et avec les opportunités de tests très limitées et les règles strictes d’amélioration des voitures, les équipes ont très peu de temps pour s’adapter au cours de la saison. Les essais de pré-saison sont limités à environ six jours, répartis sur deux à trois séances d’essais officielles. Les essais en saison sont presque inexistants, aucun essai privé n’étant autorisé et seulement quelques jours d’essais officiels disponibles.
De plus, toutes les équipes ont les mêmes voitures et moteurs en Formule 2, Formule 3 et Formule 4. Ce qui fait la différence, ce sont les compétences du pilote et les ingénieurs qui peaufinent les machines pour en tirer un peu plus de performances. Et, comme vous vous en doutez peut-être, c’est là qu’intervient l’impression 3D.
Outils et pièces personnalisés
L’impression 3D est omniprésente dans l’atelier de l’équipe – des pièces fonctionnelles et divers prototypes aux outils et gabarits astucieux. Par exemple, Arthur nous a montré un tournevis personnalisé imprimé en 3D, avec un boulon de taille différente de chaque côté et adapté à la main d’un mécanicien spécifique. Sur circuit, un détail astucieux comme celui-là peut vous faire gagner une ou deux secondes précieuses.
Un autre outil nécessaire est un refroidisseur puissant, que les mécaniciens utilisent pour refroidir le moteur entre les tours ou les séances. Le refroidisseur est un élément matériel que vous pouvez normalement acheter vous-même, mais il est amélioré grâce à l’impression 3D : notamment une pièce de montage qui s’adapte directement à l’admission du moteur de la voiture ou des supports de batterie conçus sur mesure pouvant contenir des cellules plus puissantes.
D’autres pièces imprimées en 3D peuvent être trouvées sous le capot, par exemple des tubes de circulation d’air de forme unique qui guident l’air frais vers la partie de la voiture ou du moteur où il est nécessaire. Cela permet à l’équipe de réagir à toutes les conditions pendant la course. Arthur dit que réaliser cela sans impression 3D serait très compliqué.
La partie de la voiture autour du conducteur est appelée une « zone de sécurité » et les règles stipulent que tout ce qui y est installé doit être constitué d’un matériau auto-extinguible. Par conséquent, les accessoires imprimés en 3D sont imprimés à partir de Prusament V0. Comme ce support de connecteur dans le cockpit, qui… fait quelque chose qu’Arthur ne veut pas que quiconque sache. 🙂
Cela nous amène à une remarque importante : si vous vous demandez pourquoi vous n’avez repéré aucune de ces pièces imprimées en 3D à la télévision ou dans les communiqués de presse, l’explication est simple : la plupart des pièces ou améliorations sont recouvertes de ruban adhésif imitant la texture de la fibre de carbone polie. Les équipes font cela pour protéger leur savoir-faire des autres !
Un prototypage précis fait gagner du temps
L’équipe dispose de plusieurs imprimantes 3D Original Prusa MK4 pour la production de pièces et une Original Prusa XL qui est principalement utilisée pour le prototypage. La principale raison d’utiliser des imprimantes 3D en interne est un meilleur contrôle du temps et des ressources. Au cours du processus de prototypage, ils effectuent de nombreuses itérations de leurs idées avant de réaliser la pièce finale en utilisant une autre technologie.
« Nous imprimons les pièces, les essayons, les peaufinons, les ajustons – et seulement lorsque tout fonctionne parfaitement, nous les usinons numériquement en aluminium », explique Arthur.
Souvent, ils doivent combiner plusieurs grandes pièces qui doivent s’emboîter parfaitement, ne laissant aucune place à l’imprécision.
Et c’est là que l’impression 3D leur fait gagner la partie la plus précieuse de leur emploi du temps chargé.
« Grâce au prototypage précis en utilisant l’impression 3D, nous gagnons du temps supplémentaire que nous pouvons consacrer à l’usinage numérique ou à la voiture », explique Arthur. Il y a toujours quelque chose à réparer ou à ajuster », sourit-il.
Ils utilisent également une imprimante 3D SLA – l’Original Prusa SL1S — pour prototyper des pièces petites et très détaillées, telles que des roues de boîte de vitesses ou d’autres composants importants. Par exemple, Arthur nous montre un embout de connecteur sur mesure. D’autres modèles imprimés sont soit des prototypes divers, soit des pièces flexibles qui les complètent.
Le PC-Blend Carbon Fiber est rapidement devenu leur matériau de prédilection en raison de sa résistance à la chaleur, de sa durabilité et de sa stabilité. Avec l’Original Prusa Enclosure, l’impression à partir de ces matériaux avancés est facile. Pour les prototypes simples, ils utilisent du Prusament PETG. Quant aux résines, elles utilisent la Résine Prusament Tough pour la plupart des modèles et la Flex pour les joints et les pièces mobiles.
Atelier rempli d’imprimantes Original Prusa
Arthur a commencé l’impression 3D à l’université. Il souhaitait optimiser la forme et le poids d’une voiture – pour la rendre plus performante. Contrairement à la plupart des makers, il s’est d’abord essayé à l’impression 3D métal, puis s’est tourné vers les thermoplastiques – les filaments Prusament en particulier.
Après des résultats de tests très encourageants, ils ont commencé avec une Original Prusa MK3 et en ont acquis deux autres pour suivre la production. Arthur a trouvé de plus en plus de cas d’utilisation pour l’impression 3D, ils sont donc maintenant passés à la MK4 et ont acquis l’Original Prusa XL et l’Original Prusa SL1S.
Arthur est immédiatement tombé amoureux de l’Original Prusa MK4. « L’imprimante fait tout toute seule. J’aime particulièrement la calibration automatisée de la première couche », dit-il. « La configuration est simple et facilite grandement l’ensemble du flux de travail », ajoute Arthur.
Le grand volume de construction de l’Original Prusa XL lui a ouvert de nouvelles possibilités. Il a commencé à repousser les limites et réalise désormais des prototypes avancés de plusieurs pièces automobiles importantes.
« J’aime beaucoup la XL. Elle est aussi rapide et fiable que la MK4, mais est juste plus grande », sourit Arthur.
Et une seule tête d’outil ne suffira pas. Il révèle ses projets : « Nous avons commencé avec une tête d’outil, mais maintenant j’ai décidé d’en commander une deuxième pour réaliser des modèles complexes avec des supports solubles. »
L’équipe emmène également une imprimante 3D avec elle sur le circuit – une Original Prusa MK3S+ dans une enceinte voyage avec AIX Racing à travers le monde. Pour chaque course, il y a une pièce, un composant ou un ajustement qui doit être imprimé en 3D. 🙂
Selon Arthur, l’avenir de l’impression 3D dans les courses de Formule est plus que prometteur.
« Ce n’est qu’une question de temps avant que toutes les équipes de F2 disposent d’une imprimante 3D », dit-il.
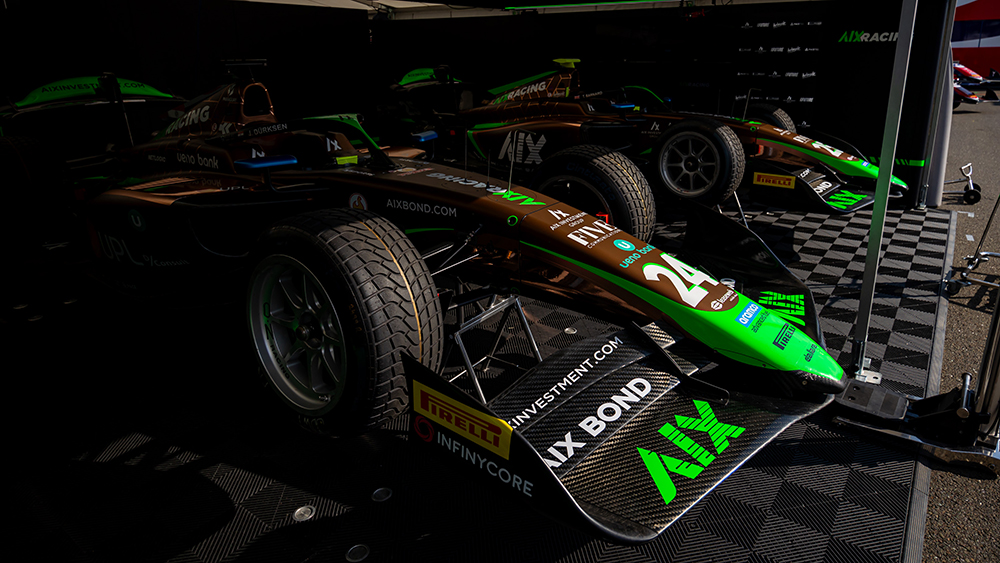
Spielberg (AUT) 27-30 juin 2024 – GP de F1 d’Autriche au Red Bull Ring.. AIX Racing F2. © 2024 Dutch Photo Agency
Jakub Kmošek, Jakub Fiedler et Štepán Feik
Vous devez vous connecter pour publier un commentaire.