Toutes les personnes impliquées dans l’impression 3D pratique ont probablement pensé à améliorer les propriétés physiques et mécaniques de leurs impressions. Vous pouvez essayer certains matériaux spéciaux, mais ceux-ci sont généralement à la fois coûteux et difficiles à imprimer. La seule autre option évidente consiste à modifier vos paramètres d’impression, ce qui a ses propres limites. Il doit certainement exister un meilleur moyen ! Eh bien … bien sûr qu’il y en a un, sinon cet article se terminerait ici. 🙂 La recuisson est un processus d’augmentation de la température pour améliorer la fermeté, la résistance à la traction et la résistance à la chaleur d’un objet donné. C’est une procédure bien connue lors de la création de pièces métalliques ou en plastique injecté. Avec les impressions 3D, c’est un peu moins connu – c’est néanmoins applicable. Étudions cela.
Comment cela fonctionne ?
En bref, nous parlons de chauffer le plastique au point où ses molécules sont capables de se réorganiser, rendant ainsi leur structure plus ferme, stable et avec moins de tension intérieure. Nous voulons atteindre la fameuse « température de transition vitreuse ». À une telle température, un objet imprimé conserve toujours sa forme mais est ramolli et il y a des changements qui se passent au niveau moléculaire, améliorant sa stabilité structurelle. Dans le chapitre suivant, nous expliquerons la nature fondamentale de ce processus d’un point de vue physique. Cela nous aidera à comprendre pourquoi exactement la recuisson contribue à améliorer la résistance mécanique et thermique, et pourquoi il est si important de trouver la température optimale. Si vous n’aimez pas beaucoup la théorie, n’hésitez pas à le sauter et à passer directement à la partie pratique, où nous présentons les résultats réels de la recuisson, en utilisant divers matériaux à différentes températures.
Structure macromoléculaire
La plupart des matériaux d’impression 3D couramment utilisés sont des polymères, c’est-à-dire de longues chaînes moléculaires répétitives. Les polymères ont deux types de structures moléculaires : amorphe (chaotique) ou semi-cristalline (partiellement organisée). Il n’y a pas de ligne de démarcation exacte, cependant, les molécules peuvent avoir différents niveaux d’agencement. Les structures cristallines sont généralement plus dures et plus rigides (similaires à un diamant, même si ce n’est pas un polymère), les polymères amorphes sont plus élastiques et flexibles. Si vous chauffez un polymère plastique à l’intérieur d’une buse, sa structure est probablement amorphe. Imaginez des spaghettis, mais avec des chaînes en polymère au lieu de pâte à pâtes. Le plastique est ensuite rapidement refroidi à température ambiante, donc sa structure reste la même. Parce qu’une pièce imprimée en 3D est principalement amorphe, sa résistance à la chaleur, sa fermeté et sa résistance à la traction sont inférieures aux matériaux cristallins avec des chaînes moléculaires organisées. Température de transition vitreuse Pour améliorer les qualités de nos impressions, nous devons réorganiser leurs chaînes moléculaires pour les rendre mieux rangées, c’est-à-dire, plus similaires aux polymères cristallins. Le niveau d’agencement plus élevé pourrait être atteint en chauffant, ou plus précisément, en atteignant la bonne température de transition vitreuse. « D’accord, alors je fais fondre un peu ce plastique et il cristallise, non ? » Hé bien oui… Mais en fait non. Si nous chauffons des matériaux cristallins, ils se liquéfient à un certain point (c’est-à-dire atteignent la liquéfaction ou simplement un point de fusion). Mais il y a une différence entre un point de fusion et une température de transition vitreuse. Les polymères amorphes n’ont pas de point de fusion exact. Au lieu de se liquéfier tout de suite, ils se ramollissent progressivement. Cette plage entre un état complètement solide et un état liquide est appelée température de transition vitreuse.
Matériau Température de transition vitreuse Température d’impression (~ fusion) PLA 65 °C (149 °F) 215 °C (419 °F) PET(G) 75 °C (167 °F) 230 °C (446 °F) ABS 105 °C (221 °F) 255 °C (491 °F)
Transformation de polymères amorphes en structure semi-cristalline
La formation de cristaux (c’est-à-dire l’organisation moléculaire) à l’intérieur des polymères ne peut se produire que lorsque la température atteint la transition vitreuse, mais reste également en dessous du point de fusion. Pour les polymères amorphes, leur point de fusion est juste après la transition vitreuse. À ce stade, la structure moléculaire se brise et les molécules commencent à se déplacer librement. Au contraire, à des températures inférieures à la transition vitreuse, les molécules sont trop « engourdies » pour se déplacer suffisamment.
Comment choisir la bonne température ?
Habituellement, les polymères amorphes ont une marge assez large entre le début de la transition vitreuse et le point de fusion. Par exemple, avec le PLA, nous parlons d’une plage de 65 à 170 °C (149 à 338 °F). Mais quelle température exacte devons-nous choisir pour des résultats optimaux ? C’est assez simple. Plus la température est élevée, plus les couches individuelles fusionnent, augmentant ainsi la fermeté de l’objet. cependant, le matériau rétrécit également, se déforme et à un certain point, il se ramollit tellement que l’objet s’effondre. De toute évidence, pour obtenir le meilleur résultat, nous devons trouver un compromis entre le maintien des dimensions et de la forme et la solidité de l’objet. Le temps de recuisson correct dépend de la taille et de la forme de l’objet. Par exemple, les échantillons que nous avons utilisés pour les tests ont été chauffés pendant 30 minutes à l’aide d’un four électrique.
Comment les différents filaments réagissent-ils à la recuisson ?
Nous avons décidé de tester 4 matériaux différents (PLA, PETG, ASA, ABS), dont 3 provenant de nos propres lignes de production (voir notre site web). Nous avons tout imprimé avec un remplissage de 100% (ceci est important pour préserver la stabilité dimensionnelle). Il y avait 4 configurations expérimentales différentes, pour trouver le meilleur matériau et la meilleure température pour la recuisson :
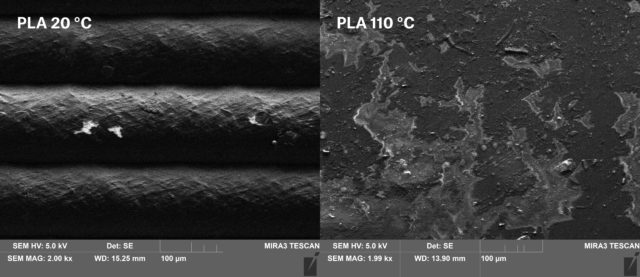
Comparaison de l’échantillon non traité et recuit de PLA; Auteur : Jiří Kmošek. Méthode : Microscope électronique à balayage. Laboratoire de faculté de restauration chimico-technologique, Université de Pardubice
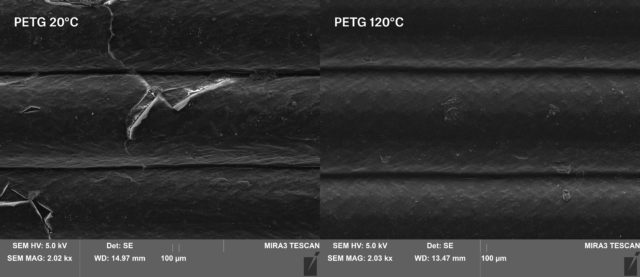
Comparaison d’un échantillon non traité et recuit de PETG ; Auteur : Jiří Kmošek. Méthode : Microscope électronique à balayage. Laboratoire de faculté de restauration chimico-technologique, Université de Pardubice


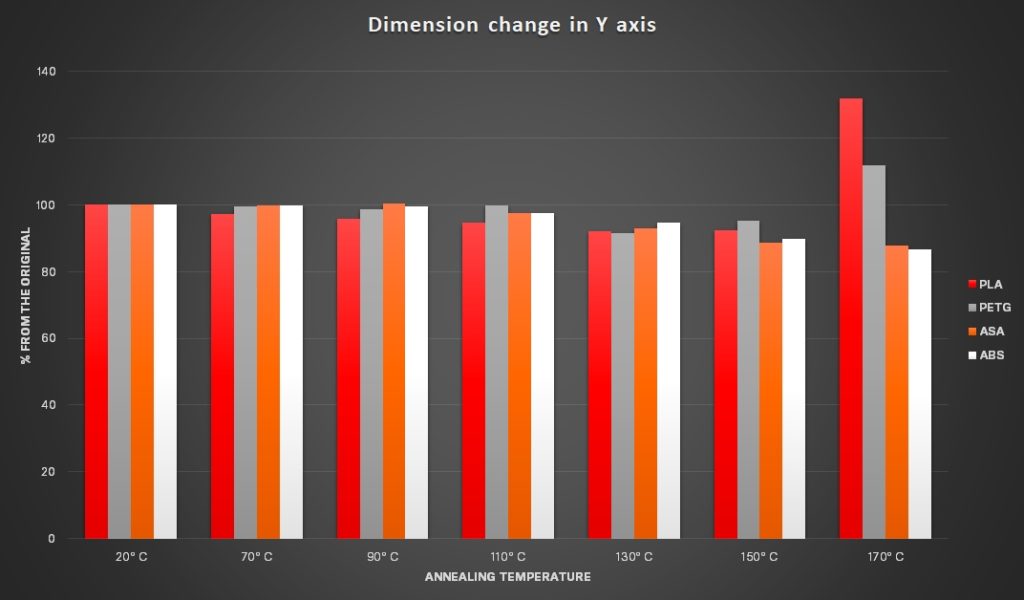
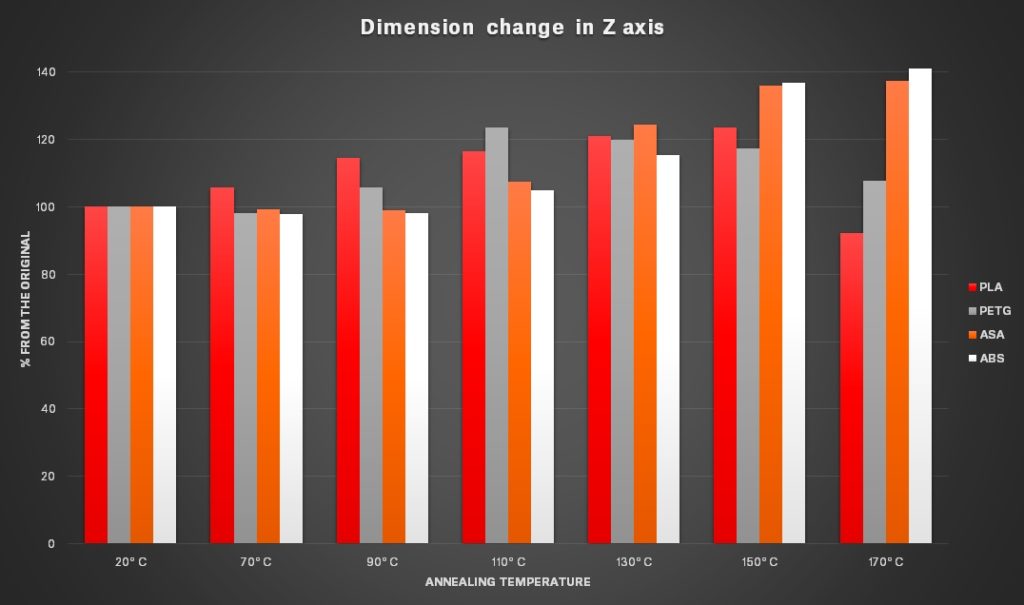
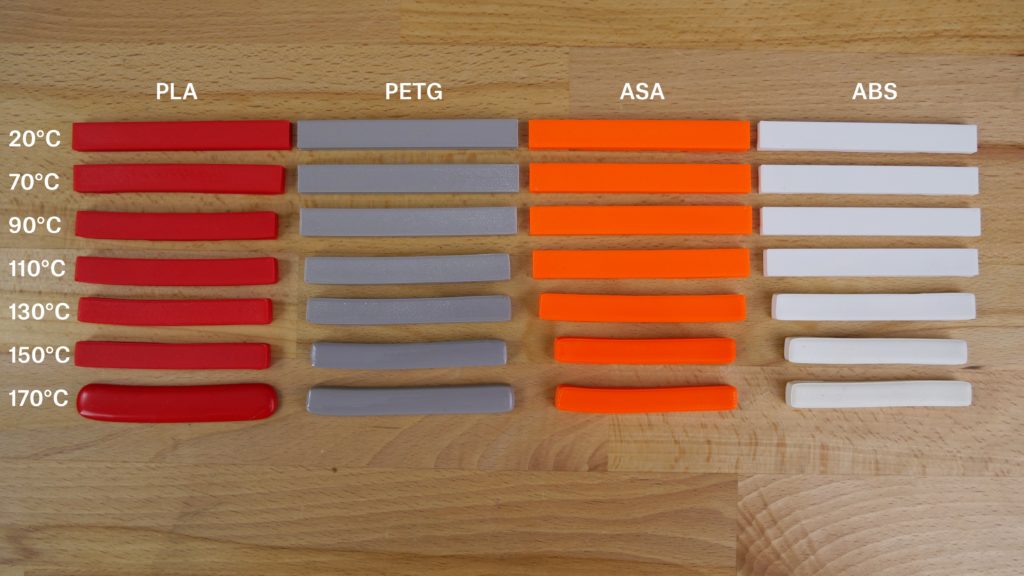
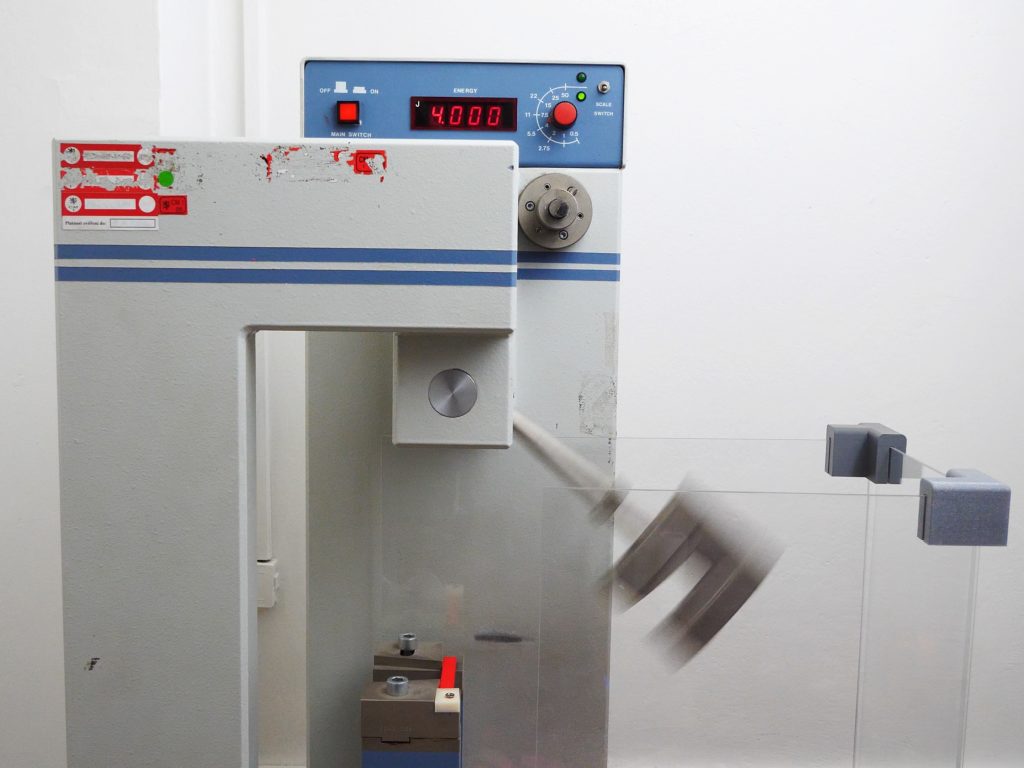
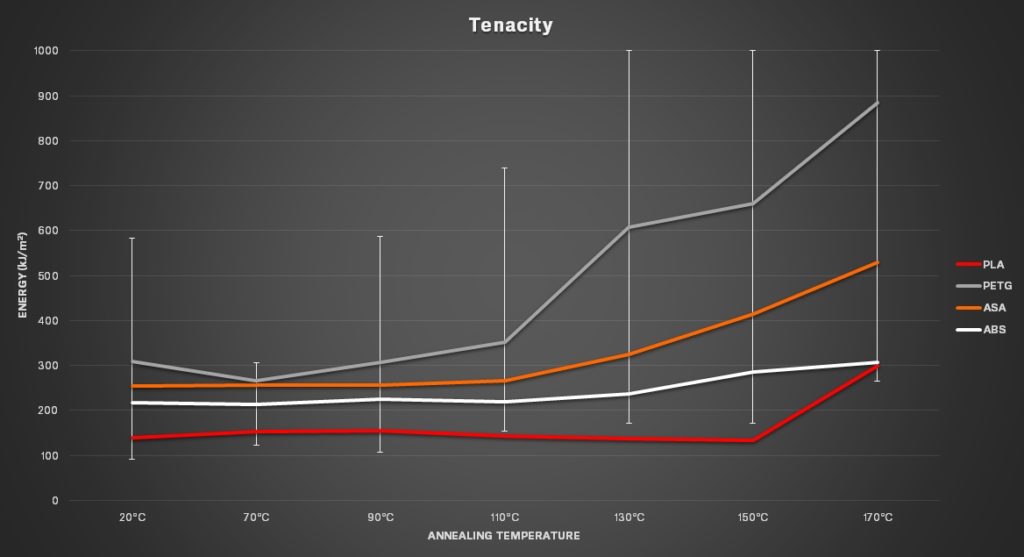
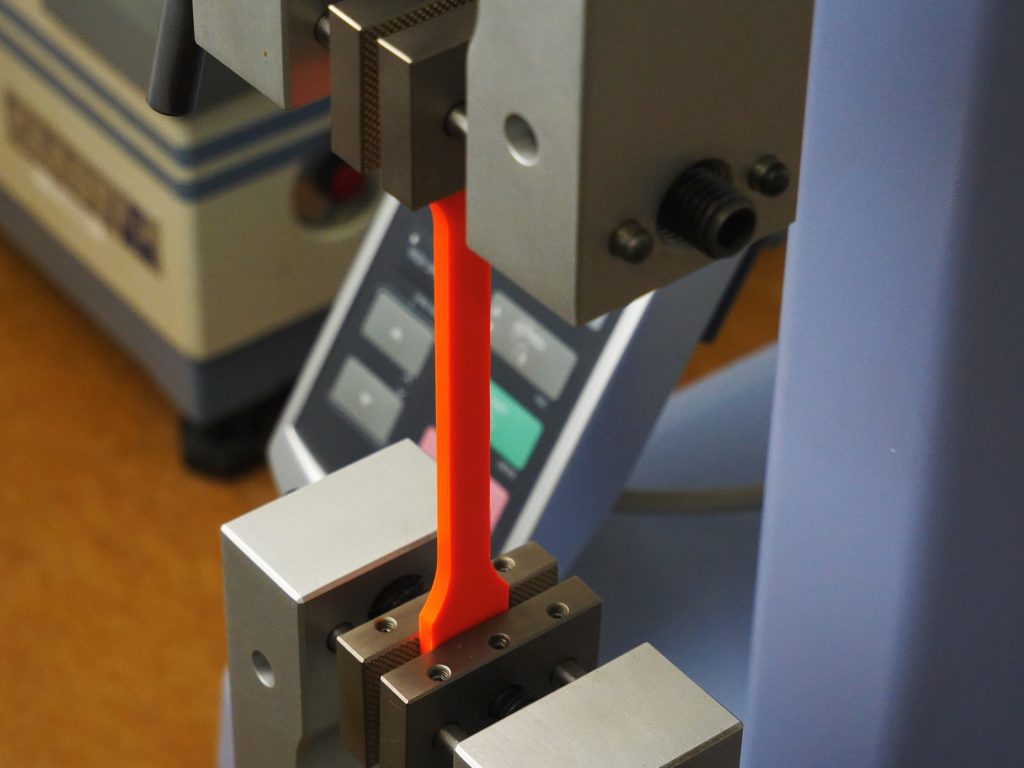
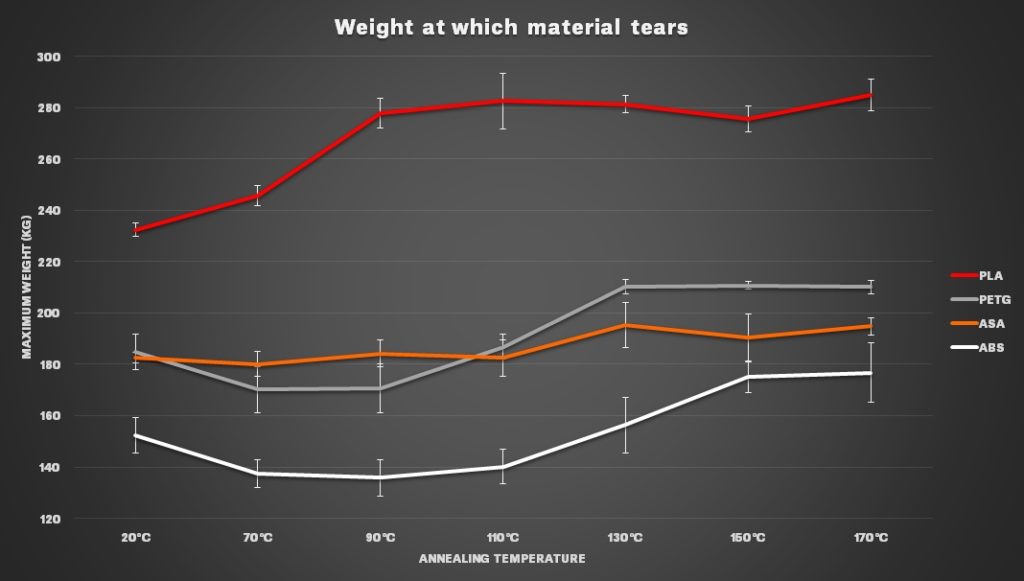
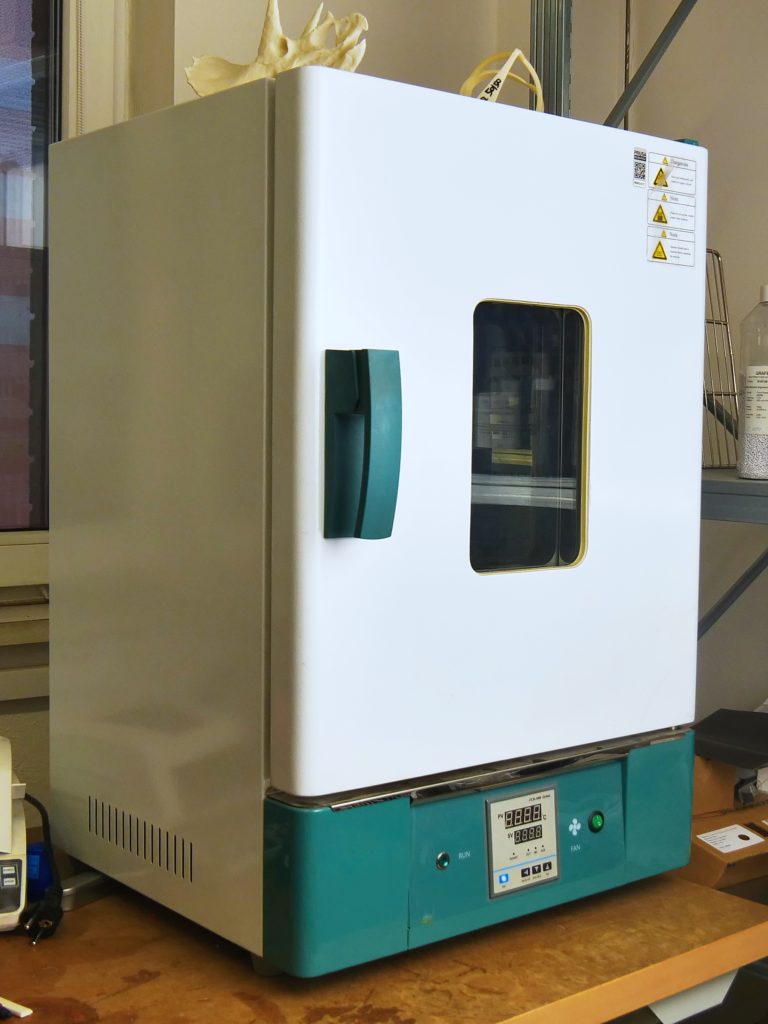
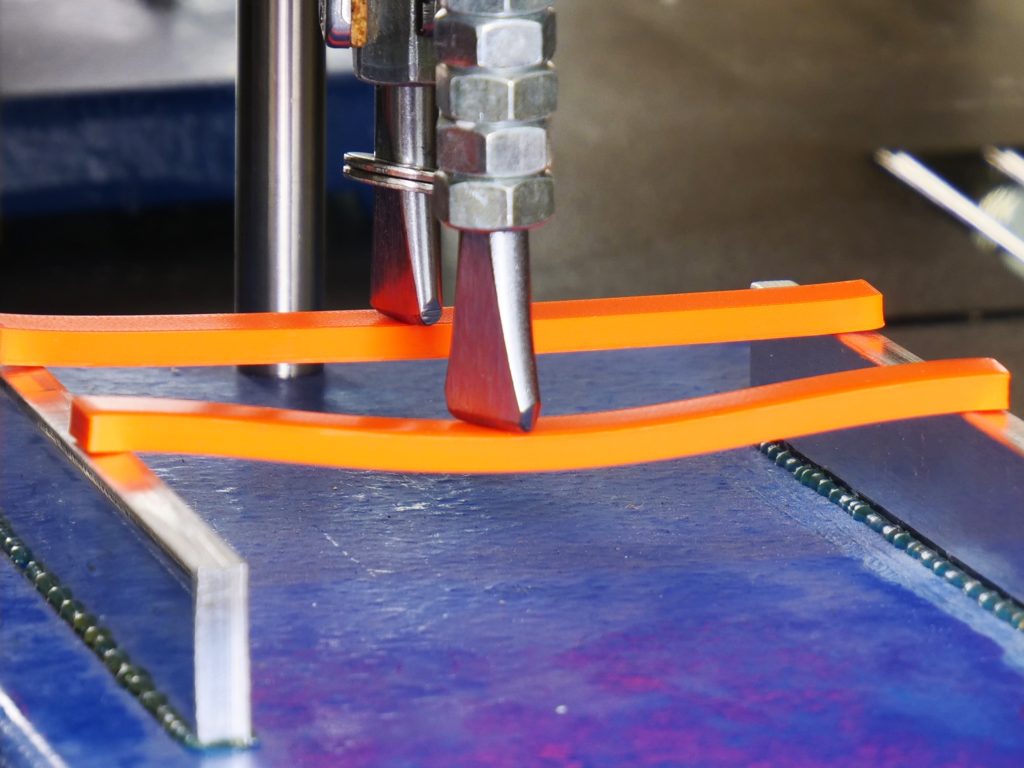
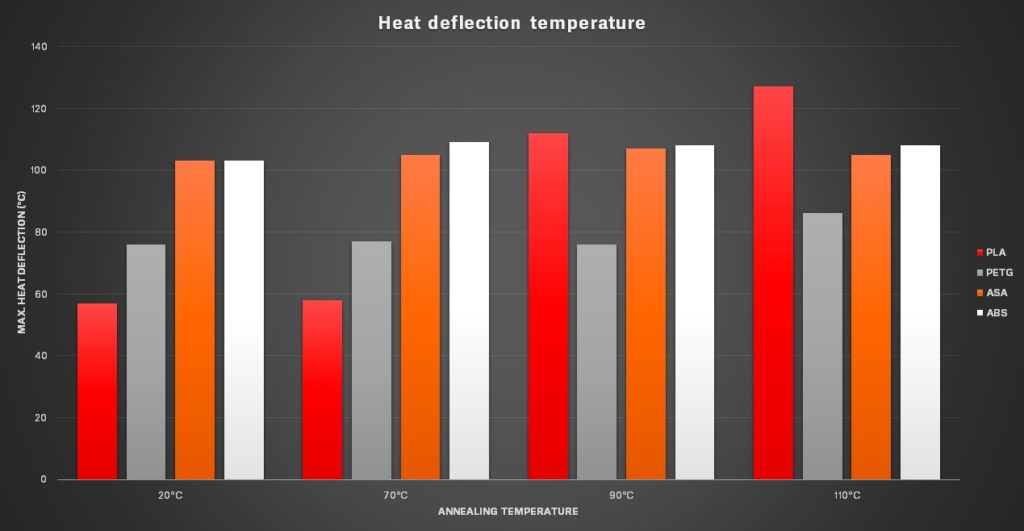
Recuisson de matériaux transparents
Attendez, notre série de tests n’est pas encore terminée. La recuisson fusionne fondamentalement les couches d’impression individuelles, non ? Donc, si vous recuisez un matériau transparent, le rendez-vous parfaitement clair ? Nous avons posé cette question nous-mêmes. Et la réponse est, en théorie, oui, mais en pratique… pas tout à fait. Nous avons essayé de recuire une petite forme circulaire en PETG, à 70-170 °C (158-338 °F). Au moment où vous atteignez (presque) une clarté totale, à quelques petites bulles de la perfection, tout s’effondre et fond complètement. Si vous utilisez des températures plus basses, la clarté reste la même que sur un modèle non traité, juste avec une déformation supplémentaire. Si vous rêviez de créer des sculptures compliquées, puis de les recuire pour qu’elles ressemblent à de la glace, vous devez choisir un chemin différent. L’ASA ou l’ABS lissés à l’acétone, impression lente avec des couches fines, etc. Plus à ce sujet ici. Exemples pratiques Nous comprenons maintenant les bases de la recuisson, connaissant à la fois ses avantages et ses inconvénients. Nous avons appris comment augmenter la durabilité mécanique et thermique et comment éviter la déformation et les changements dimensionnels. Essayons d’imprimer quelque chose d’utile et de l’améliorer avec la recuisson. Cela ne sera pas applicable dans chaque cas, nous allons donc vous montrer ce qui fonctionne et ce qui ne fonctionne pas. Notre premier exemple sont des pièces de rechange pour nos imprimantes Original Prusa i3 MK3S. Comme pour tous les tests précédents, toutes les pièces ont été imprimées avec un remplissage à 100%. Nous savons déjà que le PETG à 110 °C (230 °F) donne les meilleurs résultats, mais par curiosité, nous avons également imprimé un deuxième lot avec du PLA Prusament Lipstick Red. Le PETG a été recuit à 110 °C (230 °F), le PLA à 90 °C (194 °F), les deux pendant 45 minutes cette fois, pour s’assurer que même les plus grosses pièces chauffent complètement. Nous visions un extrudeur plus résistant mécaniquement et à la chaleur. Malheureusement, nous avons découvert que le niveau de déformation rend les deux matériaux complètement inutilisables pour de telles pièces aux formes compliquées et aux dimensions relativement précises.
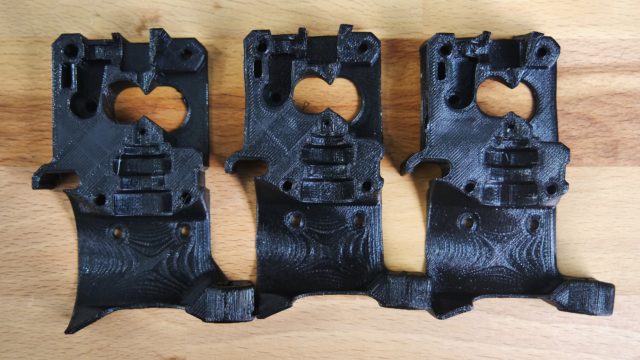
Recuisson du couvercle de l’extrudeur de l’OOriginal Prusa i3 MK3S : pièce non traitée à gauche, pièces recuites à droite.
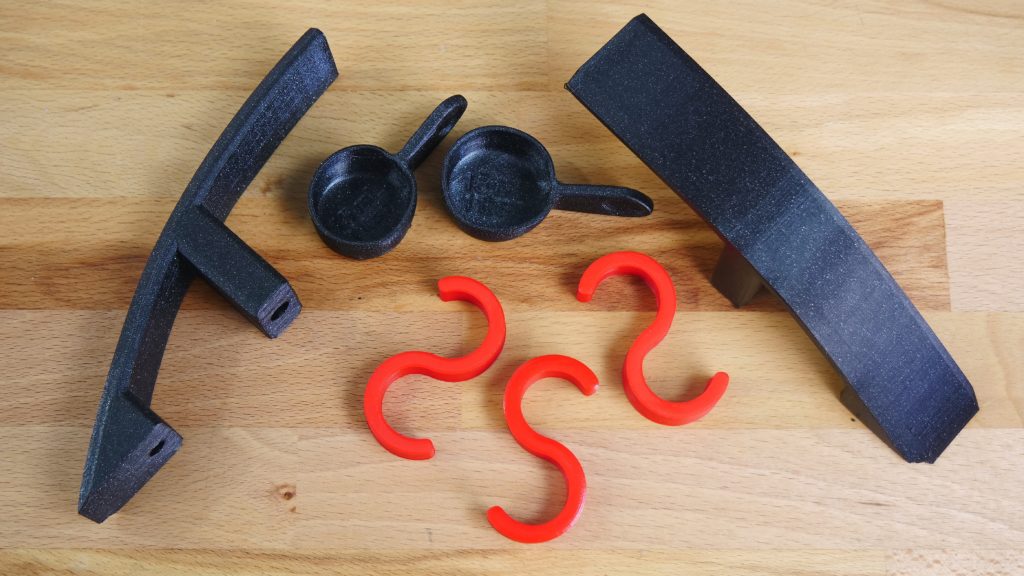
Recuire à la maison
Vous n’avez pas besoin d’un laboratoire ou d’outils dédiés pour une recuisson réussie. Un simple four à air chaud fera l’affaire. Utilisez un four électrique, mais pas un four à gaz ! Les fours à gaz sont moins sûrs, ils ne fournissent pas non plus un niveau de chaleur uniforme, souvent la température locale réelle peut être supérieure à celle que vous lisez sur le thermomètre. Placez les objets sur une assiette (vous pouvez utiliser une planche à découper), afin qu’ils ne se déforment pas et ne collent pas à vos outils ou au four. Gardez toujours un œil sur le processus ! Imaginez une pizza brûlée – eh bien, le plastique brûlé ne sent pas non plus la victoire. Nous ne prenons aucune responsabilité pour vos impressions (ou pizzas) brûlées ! 30 minutes peuvent être une bonne règle de base, mais assurez-vous d’ajuster le temps en fonction de la taille, de la forme et du matériau de l’objet concerné. Si vous avez besoin de dimensions précises, recuisez un premier lot, mesurez la quantité de rétrécissement, puis imprimez un deuxième lot mis à l’échelle en conséquence.
Conclusion
Nous avons expérimenté la recuisson de 4 matériaux différents. Alors que pour le PLA et le PETG, cette méthode est utilisable et a ses avantages (dans une certaine mesure), pour l’ASA et l’ABS, les avantages sont négligeables, tandis que la déformation et les modifications dimensionnelles atteignent des niveaux inacceptables. D’un autre côté, il est presque incroyable de voir à quel point la recuisson pourrait considérablement améliorer les caractéristiques du PLA ou du PETG. Les changements de forme et de dimension présentent toujours un inconvénient majeur, mais dans ce cas, ils sont compensés par les avantages. En particulier, le PLA a considérablement amélioré la résistance à la traction, le PETG excelle dans la durabilité aux chocs. La recuisson est une technique efficace, mais pas pour les impressions complexes et détaillées. Par exemple, vous pouvez commencer par améliorer la résistance à la traction de cintres en PLA. Ou rendre vos impressions PLA plus résistantes à la chaleur (le PLA non traité se ramollit déjà à 60 °C [140 °F]). Vous attendez-vous à ce que votre impression touche souvent le sol ? Utilisez du PETG recuit pour améliorer sa durabilité aux chocs. Rappelons que les matériaux d’impression 3D courants montrent des changements de forme et de dimensions à des températures relativement basses (70 °C [158 °F]). Si vous souhaitez conserver une forme et une taille précises, recuisez votre impression, mesurez les changements, redimensionnez-la et imprimez à nouveau. Ensuite, vous obtenez un objet à la fois avec des caractéristiques améliorées et une taille correcte. Gardez à l’esprit que si vous utilisez des pièces imprimées dans des machines, qui pourraient avoir une température de fonctionnement de 80 °C (176 °F), certaines déformations se produiront avec le temps. Avez-vous une expérience avec la recuisson ? N’hésitez pas à la partager avec nous ! Nous aimerions en savoir plus sur les nouvelles méthodes et les projets intéressants, qui pourraient être améliorés par cette astuce simple.
Bonjour ,
Afin de garantir l’absence de déformation , j’ai testé l’immersion de mon print dans de la farine de blé bien tassée par strates dans un contenant verre .
Le blocage est bon . Rapide et simple à réaliser , non toxique .
Farine T45 pour info … Elle ne semble pas changer même à 120°C .
Le tout est facile à démouler . L’aspect visuel du print est inchangé .