Wyścigi Formuły łączą w sobie emocje i akcję. W tym niezwykle konkurencyjnym świecie najmniejsze detale decydują o sukcesie lub porażce. Elitarni inżynierowie przesuwają granice technologii i próbują się nawzajem przechytrzyć, podczas gdy kierowcy starają się prowadzić samochód po idealnej linii, często ryzykując wszystko. Dzisiaj chcielibyśmy zajrzeć za kurtynę – pokazać co robi zespół AIX Racing, aby być konkurencyjnym i jak używa drukarek 3D Original Prusa, aby odnieść sukces w mistrzostwach Formuły FIA.
AIX Racing i Prusa Research intensywnie współpracowały przez ostatnie kilka lat. Nasze drukarki 3D i materiały zostały przetestowane do granic możliwości – i sprostały oczekiwaniom. Dziś możemy śmiało powiedzieć, że druk 3D robi ogromną różnicę, nawet na najwyższym poziomie sportów motorowych. Główny inżynier zespołu, Arthur Rencker, mówi:
“Druk 3D ułatwia nam wszystko.” I od razu wymienia największe zalety tej technologii: jest szybka, dokładna i niezależna od zewnętrznych dostawców.
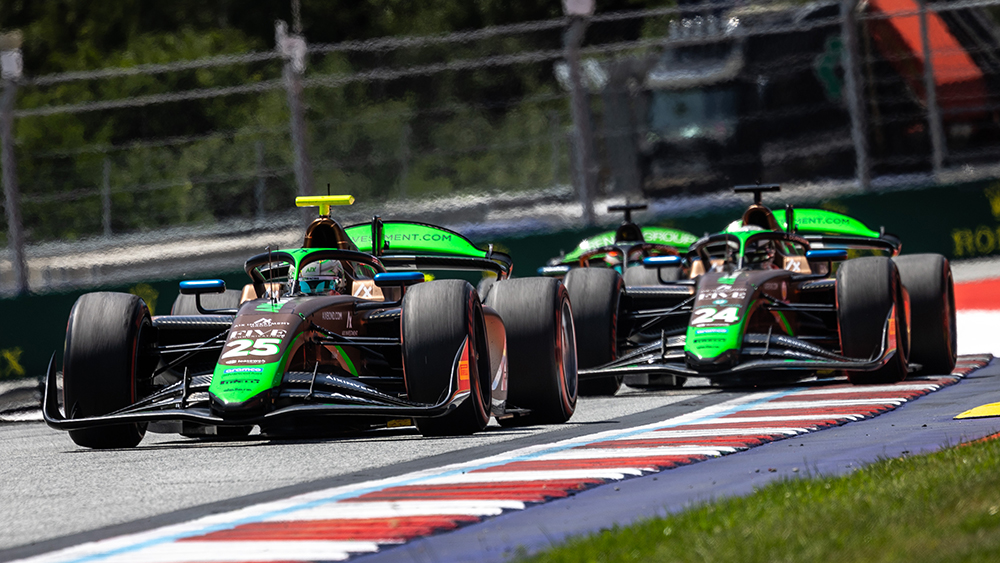
Spielberg (AT) 27. czerwca 2024 – GP Austrii F1 na torze Red Bull Ring. Taylor BARNARD #25 AIX Racing F2 © 2024 Dutch Photo Agency
Druk 3D oszczędza również czas, którego zespół zwykle nie ma zbyt wiele. W wyścigach Formuły 2 liczy się szybkość zarówno na torze, jak i w warsztacie. Co roku odbywa się 14 wyścigów F2, a przy bardzo ograniczonych możliwościach testowania i rygorystycznych zasadach usprawniania samochodów, zespoły mają bardzo mało czasu na dostosowanie się w trakcie sezonu. Testy przedsezonowe są ograniczone do około sześciu dni, rozłożonych na dwie do trzech oficjalnych sesji testowych. Testy w trakcie sezonu praktycznie nie istnieją, nie są dozwolone testy prywatne i dostępnych jest tylko kilka oficjalnych dni testowych.
Ponadto wszystkie zespoły mają takie same bolidy i silniki w Formule 2, Formule 3 i Formule 4. To, co stanowi różnicę, to umiejętności kierowcy i inżynierowie, którzy dopracowują maszyny, aby wycisnąć z nich dodatkowe osiągi. I, jak można podejrzewać, tutaj pojawia się druk 3D.
Niestandardowe narzędzia i części
Druk 3D jest wszechobecny w warsztacie zespołu – od funkcjonalnych części i różnych prototypów po sprytne narzędzia i przyrządy. Arthur pokazał nam na przykład wydrukowany w 3D niestandardowy wkrętak – dwustronny, do różnych rozmiarów śrub i dopasowany do dłoni konkretnego mechanika. Na torze wyścigowym taki sprytny szczegół może zaoszczędzić cenną sekundę lub dwie.
Kolejnym niezbędnym narzędziem jest potężna dmuchawa, której mechanicy używają do chłodzenia silnika między okrążeniami lub sesjami. Jest to sprzęt, który można normalnie kupić, ale ten jest ulepszony dzięki drukowi 3D: w szczególności część montażowa, która pasuje bezpośrednio do wlotu powietrza samochodu lub niestandardowe uchwyty na baterie, które mogą pomieścić mocniejsze ogniwa.
Inne części wydrukowane w 3D znajdziemy pod maską. Na przykład unikalnie ukształtowane kierownice powietrza, które kierują chłodne powietrze do dowolnej części samochodu lub silnika. Pozwala to zespołowi reagować na wszelkie zmiany warunków podczas wyścigu. Arthur twierdzi, że zrobienie tego bez druku 3D byłoby bardzo skomplikowane.
Obszar samochodu wokół kierowcy to „komora bezpieczeństwa”, a przepisy nakazują, aby wszystko, co jest tam zamontowane, było wykonane z samogasnącego materiału. Dlatego akcesoria są drukowane w 3D z Prusamentu V0. Na przykład to mocowanie złącza w kokpicie, które… robi coś, o czym Arthur nie chce, aby ktokolwiek wiedział. 🙂
To prowadzi nas do ważnej uwagi: jeśli zastanawiasz się, dlaczego nie można dostrzec żadnej z tych drukowanych części w telewizji lub w komunikatach prasowych, wyjaśnienie jest proste: większość elementów lub ulepszeń jest pokryta taśmą imitującą teksturę polerowanego włókna węglowego. Zespoły robią to, aby chronić swoje know-how przed innymi!
Precyzyjne prototypowanie oszczędza czas
Zespół posiada kilka drukarek 3D Original Prusa MK4 do produkcji części oraz Original Prusa XL, która jest używana głównie do prototypowania. Głównym powodem korzystania z własnych drukarek 3D jest lepsza kontrola nad czasem i zasobami. Podczas procesu prototypowania firma wykonuje wiele iteracji swoich pomysłów, zanim wykona ostateczną część przy użyciu innej technologii.
„Drukujemy części, testujemy je, dopasowujemy, korygujemy – i dopiero gdy wszystko działa idealnie, wykonujemy je z aluminium” – wyjaśnia Arthur.
Często stoi przed nimi wyzwanie połączenia kilku dużych części, które muszą idealnie do siebie pasować, nie pozostawiając miejsca na niedokładność.
I właśnie w tym miejscu druk 3D pozwala im zaoszczędzić najcenniejszą część ich napiętego harmonogramu.
„Dzięki precyzyjnemu prototypowaniu przy użyciu druku 3D zyskujemy dodatkowy czas, który możemy poświęcić na CNC lub przy samochodzie” – mówi Arthur. „Zawsze jest coś do naprawienia lub dostrojenia” – uśmiecha się.
Wykorzystują również drukarkę 3D SLA – Original Prusa SL1S – do prototypowania małych i bardzo szczegółowych części, takich jak koła przekładni lub inne ważne komponenty. Arthur pokazuje nam na przykład wykonaną na zamówienie zaślepkę złącza. Inne drukowane modele to różne prototypy lub elastyczne części, które je uzupełniają.
PC Blend Carbon Fiber szybko stał się ich ulubionym materiałem ze względu na jego odporność na temperaturę, trwałość i stabilność. Dzięki Original Prusa Enclosure drukowanie z tych zaawansowanych materiałów jest łatwe. Do prostych prototypów używają Prusamentu PETG. Jeśli chodzi o żywice, używają Prusamentu Resin Tough dla większości modeli i Flex dla przegubów i ruchomych części.
Warsztat pełen drukarek Original Prusa
Arthur po raz pierwszy podjął się druku 3D na uniwersytecie. Chciał zoptymalizować aerodynamikę i wagę samochodu, aby poprawić jego osiągi. W przeciwieństwie do większości twórców, najpierw wypróbował druk 3D z metalu, a następnie przeszedł na tworzywa termoplastyczne – w szczególności Prusament.
Po bardzo zachęcających wynikach testów, zespół zaczął od jednej Original Prusa MK3 i nabył kolejne dwie, aby nadążyć z produkcją. Arthur znajdował coraz więcej zastosowań dla druku 3D, więc teraz przeszli na MK4, a oprócz tego zakupili Original Prusa XL i Original Prusa SL1S.
Arthur od razu zakochał się w Original Prusa MK4. „Drukarka robi wszystko sama. Szczególnie podoba mi się automatyczna kalibracja pierwszej warstwy”, mówi. „Konfiguracja jest łatwa i znacznie ułatwia cały proces”, dodaje Arthur.
Duża przestrzeń robocza Original Prusa XL otworzyła przed nim nowe możliwości. Zaczął przesuwać granice i teraz tworzy zaawansowane prototypy kilku ważnych części samochodowych.
„Bardzo podoba mi się XL. Jest tak samo szybka i niezawodna jak MK4, ale po prostu większa”, uśmiecha się Arthur.
A jedna głowica narzędziowa nie wystarczy. Zdradza swoje plany: „Zaczęliśmy od jednej głowicy, ale teraz zdecydowałem się zamówić drugą, aby móc tworzyć złożone modele z rozpuszczalnymi podporami”.
Zespół zabiera również ze sobą drukarkę 3D na tor wyścigowy – Original Prusa MK3S+ w obudowie Enclosure podróżuje z AIX Racing po całym świecie. W każdym wyścigu pojawia się część, komponent lub regulacja, która musi zostać wydrukowana w 3D. 🙂
Według Arthura przyszłość druku 3D w wyścigach Formuły jest więcej niż świetlana.
„To tylko kwestia czasu, zanim wszystkie zespoły F2 będą miały drukarkę 3D” – mówi.
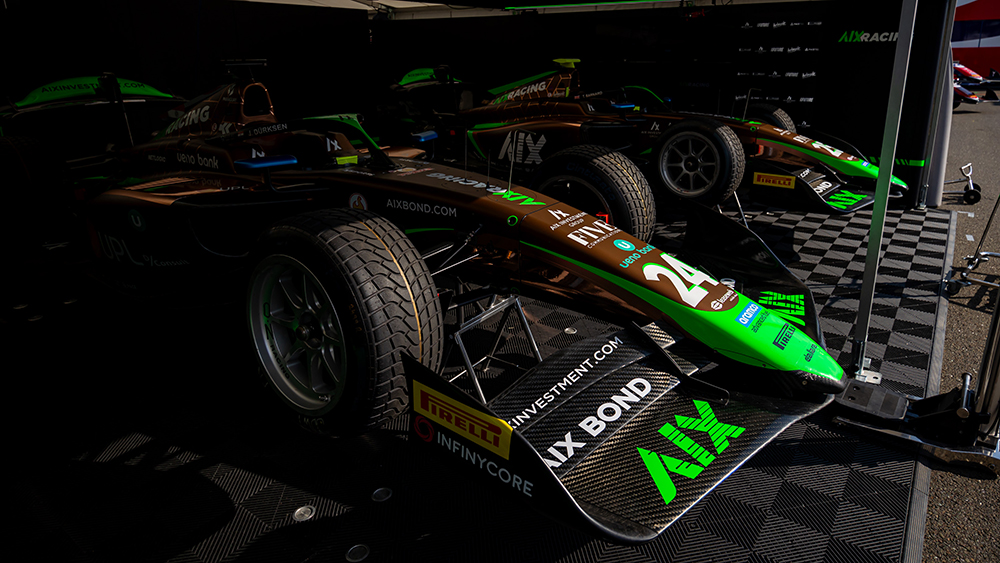
Spielberg (AT), 27-30. czerwca 2024 – Grand Prix Austrii na torze Red Bull Ring. AIX Racing F2. © 2024 Dutch Photo Agency
Jakub Kmošek, Jakub Fiedler i Štepán Feik
Musisz się zalogować, aby móc dodać komentarz.