Le gare di Formula combinano il brivido con l’azione. In questo ambiente altamente competitivo, i più piccoli dettagli determinano il confine tra il successo e il fallimento. Ingegneri d’élite spingono i limiti della tecnologia e cercano di superarsi l’un l’altro, mentre i piloti cercano di guidare l’auto alla perfezione, spesso rischiando tutto. Oggi, vorremmo portarvi dietro le quinte — che cosa fa il team di AIX Racing per essere competitivo e come sfruttano le stampanti 3D Original Prusa per raggiungere il successo nei campionati di Formula FIA.
AIX Racing e Prusa Research hanno collaborato attivamente negli ultimi anni. Le nostre stampanti 3D e i nostri materiali sono stati testati al limite e hanno superato le aspettative. Oggi possiamo affermare con sicurezza che la stampa 3D può fare un’enorme differenza, anche ai livelli più alti del motorsport. L’ingegnere capo del team, Arthur Rencker, è d’accordo:
“La stampa 3D ci facilita tutto”, afferma Arthur. E cita subito i maggiori vantaggi di questa tecnologia: è veloce, è precisa sul posto ed è indipendente da altri fornitori.
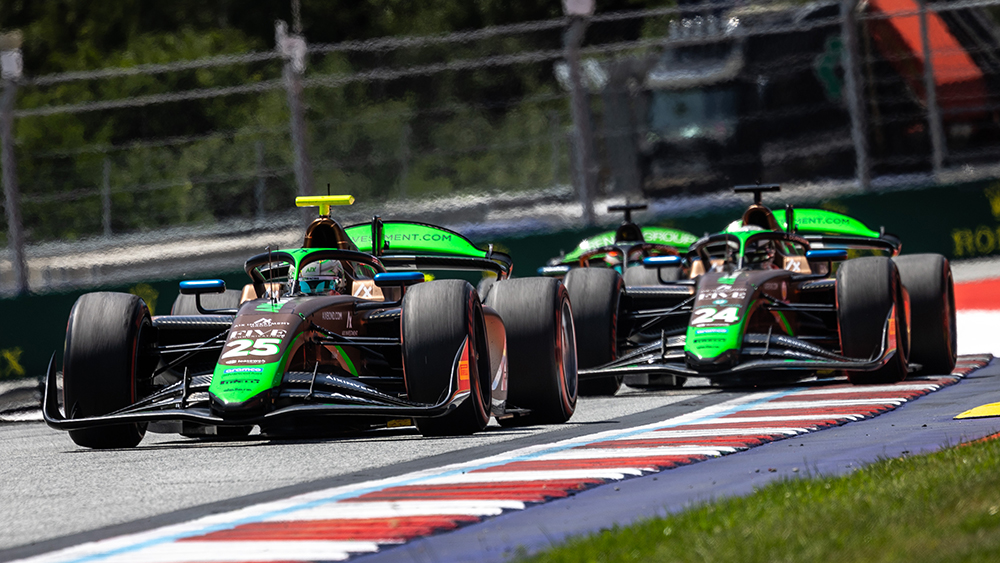
Spielberg (AUT) 27 GIUGNO – 2024 – GP d’Austria di F1 al Red Bull Ring. Taylor BARNARD #25 AIX Racing F2 © 2024 Dutch Photo Agency
La stampa 3D consente anche di risparmiare tempo, un tempo che di solito il team non ha a disposizione. Le corse di Formula si basano sulla velocità, sia in pista che in garage. Ogni anno si disputano 14 gare di F2 e, a causa delle opportunità di test molto limitate e delle rigide regole per il miglioramento della vettura, i team hanno un tempo molto limitato per adattarsi durante la stagione. I test pre-stagionali sono limitati a circa sei giorni, distribuiti in due o tre sessioni di test ufficiali. I test durante la stagione sono quasi inesistenti: non sono consentiti test privati e sono disponibili solo pochi giorni di test ufficiali.
Inoltre, tutte le squadre hanno le stesse auto e gli stessi motori in Formula 2, Formula 3 e Formula 4. Ciò che fa la differenza è l’abilità del pilota e gli ingegneri che mettono a punto le macchine per ottenere prestazioni extra. Ed è qui che, come potete immaginare, entra in gioco la stampa 3D.
Componenti e strumenti su misura
La stampa 3D è sempre presente nell’officina del team: da parti funzionali e prototipi vari a strumenti e dime intelligenti. Per esempio, Arthur ci ha mostrato un cacciavite personalizzato stampato in 3D, con una dimensione diversa per ogni lato e fatto su misura per la mano di un meccanico specifico. In pista, un dettaglio intelligente come questo può farvi risparmiare secondi preziosi.
Un altro strumento necessario è un potente sistema di raffreddamento, che i meccanici usano per raffreddare il motore tra un giro e l’altro o tra una sessione e l’altra. Il dispositivo di raffreddamento è un pezzo di hardware che si può acquistare normalmente, ma è stato migliorato con la stampa 3D: in particolare, un componente di montaggio che si adatta direttamente all’aspirazione del motore dell’auto o supporti della batteria progettati su misura che possono contenere celle più potenti.
Altre parti stampate in 3D si trovano sotto il cofano, ad esempio dei tubi per il flusso d’aria dalla forma unica che convogliano l’aria fredda in qualsiasi parte dell’auto o del motore sia necessaria. Questo permette al team di intervenire in qualsiasi condizione durante la gara. Arthur afferma che fare tutto ciò senza la stampa 3D sarebbe molto complicato.
La parte dell’auto intorno al pilota è chiamata “zona di sicurezza” e le regole impongono che tutto ciò che vi è installato sia realizzato in materiale autoestinguente. Pertanto, gli accessori sono stampati in 3D con Prusament V0. Come questo supporto per connettore nella cabina di guida, che serve a… qualcosa che Arthur non vuole far sapere a nessuno. 🙂
Questo ci porta a una nota importante: se vi state chiedendo perché non avete visto nessuna di queste parti stampate in 3D in TV o nei comunicati stampa, la spiegazione è semplice: La maggior parte delle parti o dei miglioramenti sono coperti da un nastro che simula la struttura in fibra di carbonio lucida. I team lo fanno per proteggere il loro know-how da altri!
Una prototipazione precisa per risparmiare tempo
Il team dispone di diverse stampanti 3D Original Prusa MK4 per la produzione di componenti e di una Original Prusa XL usata principalmente per la prototipazione. La ragione principale dell’utilizzo di stampanti 3D in-house è legata a un migliore controllo dei tempi e delle risorse. Durante il processo di prototipazione, realizzano molte iterazioni delle loro idee prima di creare il pezzo finale utilizzando un’altra tecnologia.
“Stampiamo i pezzi, li proviamo, li mettiamo a punto, li regoliamo – e solo quando tutto funziona perfettamente, allora li realizziamo a partire dall’alluminio”, spiega Arthur.
Spesso è necessario combinare più parti di grandi dimensioni che devono combaciare perfettamente, senza lasciare spazio a imprecisioni. Ed è qui che la stampa 3D consente di recuperare il tempo più prezioso da dedicare ai loro impegni.
“Grazie alla prototipazione precisa con la stampa 3D, guadagniamo tempo extra da dedicare al CNC o alla vettura”, afferma Arthur. C’è sempre qualcosa da aggiustare o mettere a punto”, sorride. Utilizzano anche una stampante 3D SLA — la Original Prusa SL1S — per prototipare parti piccole e molto dettagliate, come le ruote dei riduttori o altri componenti importanti. Ad esempio, Arthur ci mostra un tappo di chiusura di un connettore realizzato su misura. Altri modelli stampati sono vari prototipi o parti flessibili che li completano.
Il PC-Blend Carbon Fiber è diventato presto il loro materiale preferito grazie alla sua resistenza al calore, alla durata e alla stabilità. Grazie alla Original Prusa Enclosure, stampare questi materiali avanzati è facilissimo. Per dei semplici prototipi, utilizzano il Prusament PETG. Per quanto riguarda le resine, usano la resina Prusament Resin Tough per la maggior parte dei modelli e la resina Flex per giunti e parti mobili.
Un laboratorio pieno di stampanti Original Prusa
Arthur ha iniziato a stampare in 3D all’università. Voleva ottimizzare la forma e il peso di un’auto, per migliorarne le prestazioni. A differenza della maggior parte dei maker, ha iniziato con la stampa 3D in metallo per poi passare ai materiali termoplastici, in particolare ai filamenti Prusament. Dopo aver ottenuto risultati molto incoraggianti, hanno iniziato con una Original Prusa MK3 e ne hanno acquistate altre due per tenere il passo con la produzione. Arthur ha poi trovato sempre più casi d’uso per la stampa 3D, quindi è passato a Original Prusa MK4 e ha acquistato anche una Original Prusa XL e Original Prusa SL1S.
Arthur si è subito innamorato della Original Prusa MK4. “La stampante fa tutto da sola. Mi piace soprattutto la calibrazione automatica del primo strato”, afferma. “L’impostazione è semplice e rende l’intero flusso di lavoro molto più facile”, aggiunge.
L’ampio volume di stampa della Original Prusa XL gli ha aperto nuove possibilità. Ha iniziato a spingersi oltre i limiti e ora realizza prototipi avanzati di diversi componenti automobilistici importanti. “Mi piace molto la XL. È veloce e affidabile come la MK4, ma più grande”, sorride Arthur.
E la testina singola non sarà sufficiente, svelandoci i suoi piani: “Abbiamo iniziato con una sola testina, ma adesso ho deciso di ordinarne una seconda per realizzare modelli complessi con supporti solubili.”
Il team porta con sé una stampante 3D anche in pista: una Original Prusa MK3S+ in enclosure viaggia con AIX Racing in tutto il mondo. A ogni gara c’è un pezzo, un componente o una regolazione che deve essere stampata in 3D. 🙂
Secondo Arthur, il futuro della stampa 3D nelle corse di Formula è più che roseo.
“È solo una questione di tempo prima che tutti i team di F2 abbiano una stampante 3D”, afferma.
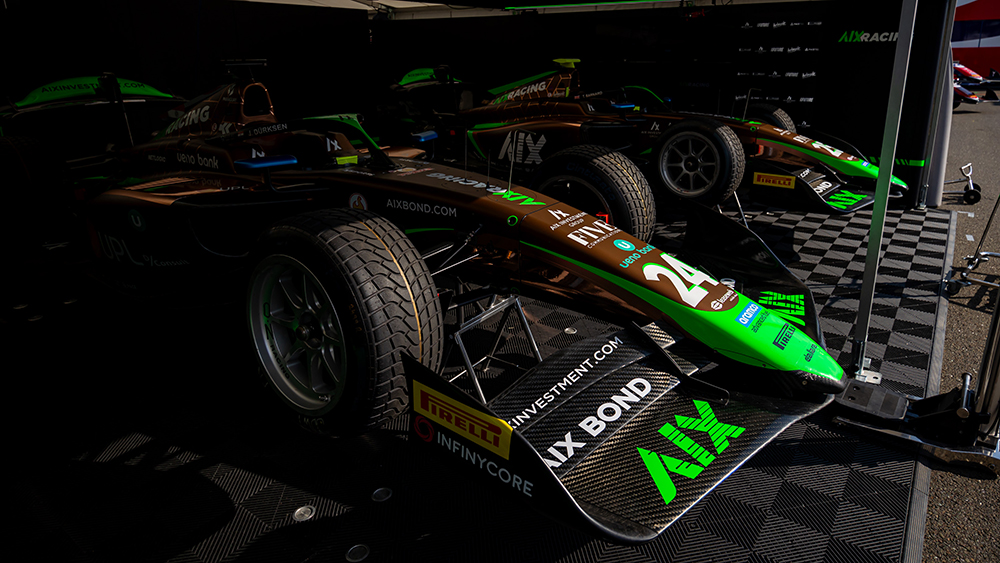
Spielberg (AUT), 27-30 LUGLIO 2024 – Gran Premio d’Austria al Red Bull Ring. AIX Racing F2. © 2024 Dutch Photo Agency
Jakub Kmošek, Jakub Fiedler and Štepán Feik
Devi essere connesso per inviare un commento.