Nous pourrions imprimer en 3D de nombreuses choses différentes, et toutes ne doivent pas être des produits finaux. Au lieu de cela, nous pourrions créer divers outils, modèles, conteneurs… ou des moules. Cette dernière possibilité est le sujet de notre article. Nous vous montrerons comment mouler des matériaux tels que de la cire ou du savon, dans des conditions domestiques en utilisant des outils facilement disponibles. Notre objectif est de prouver que le moulage avec des moules en silicone est beaucoup plus facile qu’il n’y paraît à première vue. Mes propres tentatives ont inclus quelques essais et erreurs avant d’apprendre les bonnes méthodes. Par conséquent, j’espère que je peux maintenant aider les autres à économiser du matériel, du temps et des efforts. Remarque : Les images ci-dessous montrent que j’ai utilisé une vieille feuille d’impression PEI comme tapis de travail. Cela n’a pas de but particulier, utilisez à peu près n’importe quoi d’autre à la place – ne risquez pas d’endommager votre feuille d’impression parfaitement utilisable 🙂
Matériau pour la fabrication de moules
Pour créer le moule, nous utiliserons un caoutchouc silicone à deux composants, polymérisé par condensation. Dans notre cas, c’est un produit local fabriqué en République Tchèque appelé Lukopren N Super, mais il existe de nombreux produits similaires que vous pourriez probablement trouver disponibles dans le monde, par exemple, Smooth-on, ACC Silicones, RTV, etc. Le Lukopren se compose de la partie A (le silicone lui-même) et de la partie B (durcisseur/activateur) et il durcit à température ambiante, en environ 24 heures. Le temps de durcissement est affecté par la quantité de durcisseur et la température ambiante. Le moule résultant a une forme stable et est à la fois résistant chimiquement et thermiquement. Vous pouvez l’utiliser pour mouler de nombreux matériaux, y compris du polyuréthane, de l’époxyde, du polyester, du plâtre, du béton, du ciment, de la cire, des alliages à bas point de fusion ou du savon. Ce matériau de moule convient à la fois aux petits moulages détaillés et aux gros objets (c.-à-d. les statues). Aucune pompe à vide n’est nécessaire en raison de son excellente fluidité et de sa faible viscosité. Le caoutchouc silicone peut être à la fois coulé ou brossé (avec un épaississant ajouté dans le mélange), bien qu’il existe de meilleures options de brossage comme par exemple le Smooth-on mentionné ci-dessus. Le moulage de métal sera décrit en détail dans notre prochain article, axé sur la fabrication de bijoux et les applications dentaires.
Le modèle
Pour obtenir un moule de qualité, nous avons d’abord besoin d’un modèle père de qualité pour créer le moule. La conception d’un tel modèle peut être fastidieuse et nécessiter une certaine patience et une grande attention aux détails, surtout si nous sommes nouveaux dans les applications de modélisation 3D. Vous pouvez ignorer cette partie en téléchargeant simplement un modèle prêt à l’emploi à partir d’une base de données Internet, telle que www.prusaprinters.org. Faites attention aux fameux surplombs – les contours du modèle qui ont un angle plus important qu’un angle droit (90°) par rapport au plan de séparation du moule. En d’autres termes, si vous regardez dans un moule directement par le haut, vous devriez pouvoir voir la surface intérieure entière, sans rien de caché « derrière un coin ». Ces surplombs pourraient par la suite faire coincer le modèle père ou le moulage final dans le moule. Heureusement, l’un des grands avantages du caoutchouc silicone est son élasticité – il se déformera un peu lorsque nous le plierons et le tordrons pour retirer le moulage fini. Cela signifie que nous pourrions nous permettre un certain niveau de surplomb. Le modèle correctement moulé devrait sortir presque spontanément, après juste une légère pression sur le moule. Si nous utilisons une méthode de moulage à cire perdue, nous n’avons pas du tout à nous soucier des surplombs, car nous ne retirons pas le modèle, il est détruit à l’intérieur du moule. Pour la fabrication de moules en caoutchouc silicone, tout matériau non poreux convient pour un modèle père. Cela signifie que vous pouvez utiliser des impressions 3D à partir de filaments ou de résine. Les couches d’impression ne sont pas un problème (en termes de retrait du moule), mais elles seront bien sûr visibles sur le moulage final. Cela signifie que l’impression à partir de résine est plus appropriée – j’ai utilisé l’imprimante Original Prusa SL1. Pour le moulage à cire perdue, il existe des résines de moulage spéciales, qui peuvent être complètement fondues ou brûlées hors du moule. Plus d’informations sur cette méthode seront également disponibles dans le prochain article. Le modèle père imprimé en 3D est beaucoup plus utilisable qu’un fait à la main. Dans le pire des cas, si nous l’endommagions d’une manière ou d’une autre lors de notre première tentative de fabrication de moule, nous pourrions toujours l’imprimer à nouveau. Inspectez soigneusement la surface du modèle père avant de l’utiliser pour la fabrication de moules. Traitez les petites imperfections, éraflures, restes de support ou même les empreintes digitales ! Sinon, tous ces défauts de surface seront copiés dans le moualge final !
Préparation finale pour la fabrication du moule
Avant de fabriquer le moule en deux parties, nous devons définir son plan de division. Nous couperons le canal de coulée et les bouches d’aération dans le moule plus tard avant le moulage lui-même. Le plan de division sera créé comme suit : poussez le modèle père dans la pâte à modeler jusqu’au niveau du plan de division prévu (il ne doit pas nécessairement être strictement horizontal). Pour pouvoir aligner correctement les deux moitiés de moule ultérieurement, créez ce que l’on appelle des clés d’enregistrement.
Il peut s’agir de simples trous réalisés à l’aide d’un manche de pinceau, de rainures sculptées – tout ce qui perturbe la surface lisse, ce qui pourrait faire glisser les moitiés du moule. Nous devons également créer une coque extérieure qui retiendra le silicone liquide à l’intérieur et l’empêchera de couler sur toute la table. Après avoir exploré quelques impasses à l’aide de briques Lego ou de divers blocs assemblés avec un pistolet à colle, nous avons trouvé une solution simple, propre, mais pas si évidente (hmm …) – nous l’avons imprimée en 3D sur la Original Prusa i3 MK3S :). Des paroies de 4 périmètres d´épaisseur ont rendu la coque suffisamment solide.
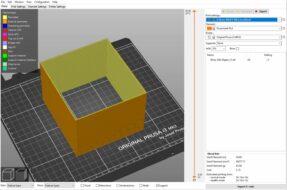
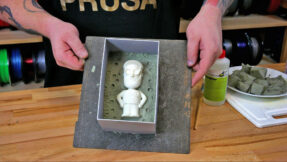
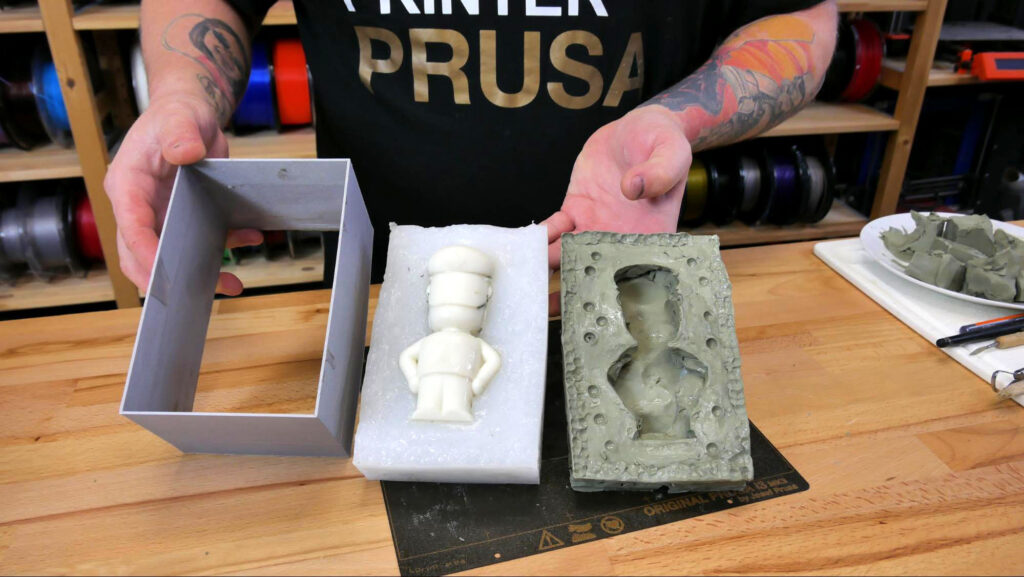
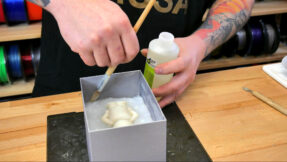
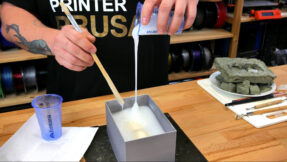
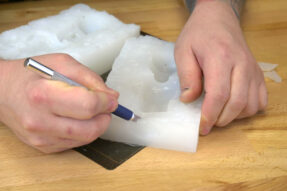
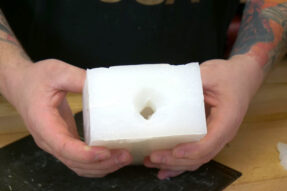
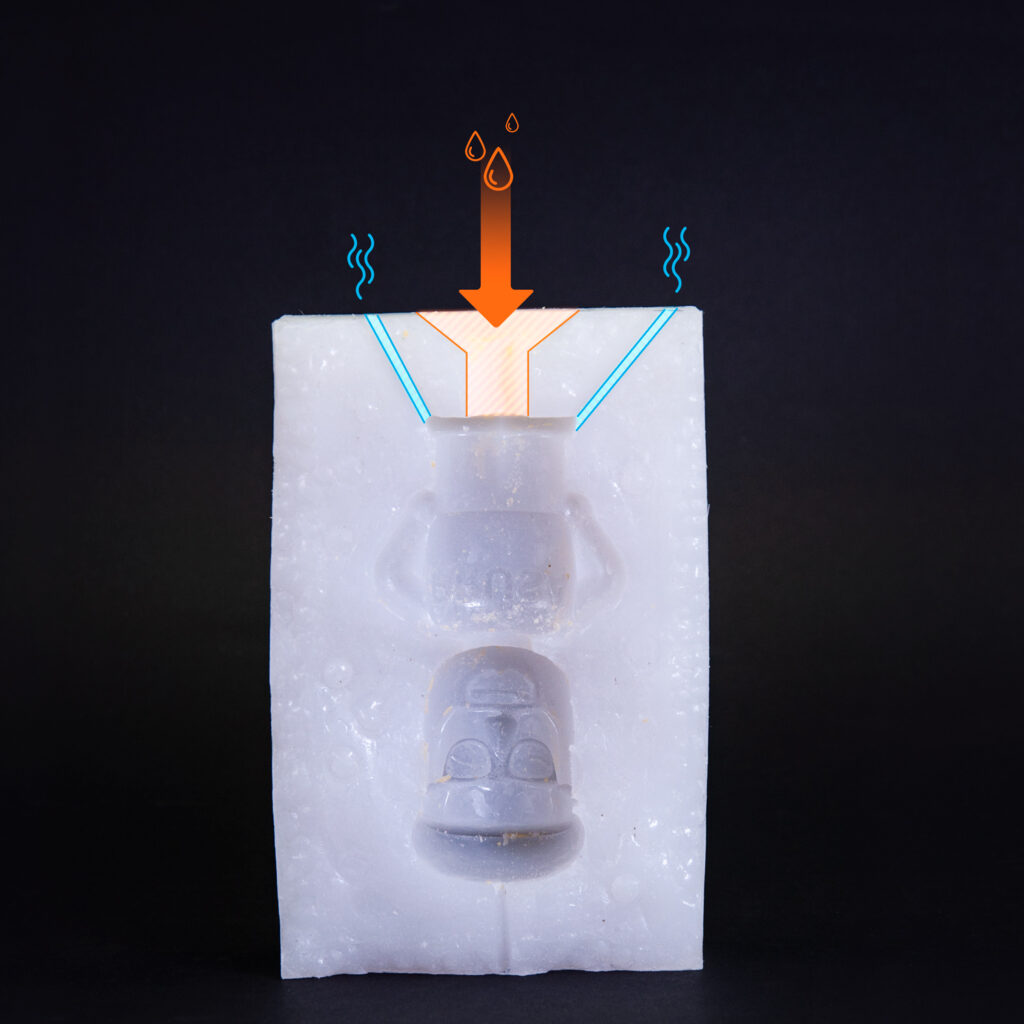
Processus de moulage
Nous avons un moule complet comprenant un canal de coulée et des prises d’air. Notez que le moule pourrait être réutilisé plusieurs fois, vous pouvez faire jusqu’à 30 à 50 moulages, selon le niveau de détail des contours. Il est maintenant temps pour le moulage lui-même. Encore une fois, nous utilisons l’agent de démoulage pour couvrir les surfaces internes du moule – assurez-vous que vous êtes vraiment minutieux, sinon le plâtre pourrait coller au moule. Nous moulerons du savon et de la cire. Pour le moulage avec du savon, nous devons d’abord liquéfier le matériau en le chauffant. Vous pouvez utiliser un four à micro-ondes ordinaire avec les réglages maximum, pendant environ une minute (cela dépend de la puissance du four à micro-ondes et du matériau de savon exact que vous utilisez). Pour être prudent, nous vous recommandons de vérifier la situation toutes les 30 secondes. Scotchez les deux moitiés du moule étroitement ensemble. Versez lentement le matériau chaud dans le moule. Il se solidifiera en environ 1-3 heures, selon la température ambiante (vous pouvez le mettre au réfrigérateur pour accélérer les choses).
Le même processus pourrait être utilisé pour couler de la cire de bougie, la seule étape supplémentaire est de découper une rainure pour la mèche de bougie, à l’extrémité opposée du canal de coulée.
Insérez la mèche et versez la cire (encore une fois, fondue au micro-ondes) dans le moule. La cire se solidifie plus rapidement que le savon et est prête à être retirée du moule en 30-60 minutes environ (encore une fois, en fonction de la température ambiante). Assurez-vous de remplir complètement le canal de coulée, car la cire a tendance à rétrécir lors du refroidissement.
Conclusion
La fabrication de moules n’est pas un processus difficile, elle vous permet de multiplier facilement vos impressions 3D, en utilisant différents matériaux. Vous pourriez même démarrer une chaîne de production à court terme ! Alors, bonne chance avec votre passe-temps et comme toujours, bonne impression !
Vous devez vous connecter pour publier un commentaire.