Der Formel-Rennsport verbindet Spannung und Action. In dieser hart umkämpften Welt entscheiden die kleinsten Details über Erfolg und Misserfolg. Elite-Ingenieure gehen an die Grenzen der Technologie und versuchen, sich gegenseitig zu übertrumpfen, während die Fahrer versuchen, das Auto perfekt zu steuern und dabei oft alles riskieren. Heute möchten wir Ihnen einen Blick hinter den Vorhang gewähren – was das AIX Racing Team tut, um wettbewerbsfähig zu sein, und wie es Original Prusa 3D-Drucker einsetzt, um in den FIA-Formelmeisterschaften erfolgreich zu sein.
AIX Racing und Prusa Research haben in den letzten Jahren ausgiebig zusammengearbeitet. Unsere 3D-Drucker und Materialien wurden bis zum Äußersten getestet – und haben den Erwartungen standgehalten. Heute können wir mit Sicherheit sagen, dass der 3D-Druck einen großen Unterschied macht, selbst auf der höchsten Ebene des Motorsports. Der Chefingenieur des Teams, Arthur Rencker, sagt:
„Der 3D-Druck macht alles einfacher für uns“, sagt Arthur. Und er nennt auch gleich die größten Vorteile dieser Technologie: Sie ist schnell, vor Ort präzise und unabhängig von zusätzlichen Lieferanten.
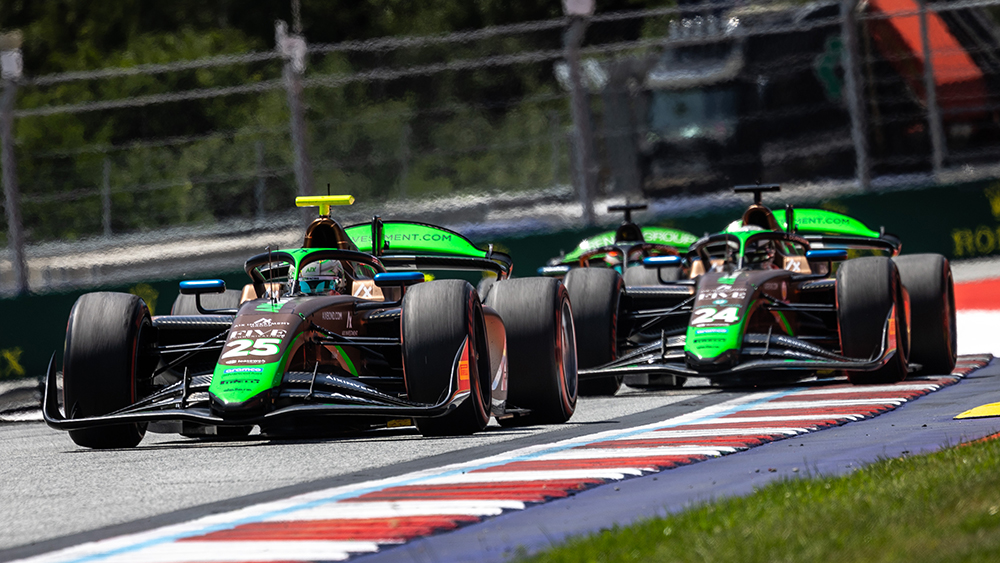
Spielberg (AUT) 27-JUN 2024 – F1 Österreich GP auf dem Red Bull Ring. Taylor BARNARD #25 AIX Racing F2 © 2024 Dutch Photo Agency
Außerdem spart der 3D-Druck Zeit, von der das Team normalerweise nicht viel hat. Beim Formel-Rennsport geht es um Geschwindigkeit, sowohl auf der Rennstrecke als auch in der Garage. Jährlich finden 14 F2-Rennen statt, und aufgrund der stark eingeschränkten Testmöglichkeiten und der strengen Regeln für die Verbesserung der Autos haben die Teams nur sehr wenig Zeit, um sich während der Saison anzupassen. Die Tests vor der Saison beschränken sich auf etwa sechs Tage, die sich auf zwei bis drei offizielle Testsitzungen verteilen. Während der Saison gibt es so gut wie keine Tests, da keine privaten Tests erlaubt sind und nur wenige offizielle Testtage zur Verfügung stehen.
Außerdem haben alle Teams in der Formel 2, Formel 3 und Formel 4 die gleichen Autos und Motoren. Was den Unterschied macht, ist das Können des Fahrers und der Ingenieure, die die Maschinen fein abstimmen, um ein bisschen mehr Leistung aus ihnen herauszuholen. Und, wie Sie vielleicht vermuten, kommt hier der 3D-Druck ins Spiel.
Maßgeschneiderte Werkzeuge und Teile
Der 3D-Druck ist in der Werkstatt des Teams allgegenwärtig – von Funktionsteilen und verschiedenen Prototypen bis hin zu cleveren Werkzeugen und Vorrichtungen. Arthur zeigte uns zum Beispiel einen 3D-gedruckten Schraubenzieher – mit einer unterschiedlich großen Schraubengröße auf jeder Seite und maßgeschneidert für die Hand eines bestimmten Mechanikers. Auf der Rennstrecke kann so ein cleveres Detail ein oder zwei wertvolle Sekunden sparen.
Ein weiteres notwendiges Werkzeug ist ein leistungsstarker Kühler, den die Mechaniker verwenden, um den Motor zwischen den Runden oder Sitzungen abzukühlen. Der Kühler ist ein Hardwareteil, das Sie normalerweise selbst kaufen können, das aber durch 3D-Druck verbessert wird: insbesondere ein Befestigungsteil, das direkt an den Ansaugstutzen des Fahrzeugmotors passt, oder speziell entworfene Batteriehalter, die leistungsstärkere Zellen aufnehmen können.
Andere 3D-gedruckte Teile befinden sich unter der Motorhaube, z.B. einzigartig geformte Luftstromrohre, die die kühle Luft zu dem Teil des Autos oder des Motors leiten, wo sie gerade benötigt wird. So kann das Team auf alle Bedingungen während des Rennens reagieren. Arthur sagt, dass dies ohne den 3D-Druck sehr kompliziert wäre.
Der Teil des Autos, der den Fahrer umgibt, wird als „Sicherheitszone“ bezeichnet, und die Vorschriften schreiben vor, dass alles, was dort installiert wird, aus selbstverlöschendem Material sein muss. Daher wird 3D-gedrucktes Zubehör aus Prusament V0 gedruckt. Wie dieser Anschlusshalter im Cockpit, der… etwas tut, von dem Arthur nicht möchte, dass es jemand weiß 🙂
Das bringt uns zu einem wichtigen Hinweis: Wenn Sie sich fragen, warum Sie keines dieser 3D-gedruckten Teile im Fernsehen oder in Pressemitteilungen gesehen haben, ist die Erklärung einfach: Die meisten Teile oder Verbesserungen sind mit einer Folie überzogen, die eine polierte Karbonfasertextur imitiert. Die Teams tun dies, um ihr Know-how vor anderen zu schützen!
Präzises Prototyping spart Zeit
Das Team verfügt über mehrere Original Prusa MK4 3D-Drucker für die Teileproduktion und einen Original Prusa XL, der hauptsächlich für das Prototyping verwendet wird. Der Hauptgrund für die Verwendung von 3D-Druckern im eigenen Haus ist die bessere Kontrolle über Zeit und Ressourcen. Während des Prototyping-Prozesses machen sie viele Iterationen ihrer Ideen, bevor sie das endgültige Teil mit einer anderen Technologie herstellen.
„Wir drucken die Teile, probieren sie aus, stimmen sie ab, passen sie an – und erst wenn alles perfekt funktioniert, fertigen wir sie mit CNC aus Aluminium“, erklärt Arthur.
Oft müssen sie mehrere große Teile kombinieren, die perfekt zusammenpassen müssen und keinen Raum für Ungenauigkeiten lassen.
Und genau da spart ihnen der 3D-Druck den wertvollsten Teil ihres vollen Terminkalenders.
„Dank des präzisen Prototyping mit 3D-Druck gewinnen wir zusätzliche Zeit, die wir mit der CNC oder dem Auto verbringen können“, sagt Arthur. Es gibt immer etwas zu reparieren oder zu tunen“, lächelt er.
Sie setzen auch einen SLA 3D-Drucker ein – denOriginal Prusa SL1S – um kleine und sehr detaillierte Teile wie Getrieberäder oder andere wichtige Komponenten zu prototypisieren. Arthur zeigt uns zum Beispiel eine maßgefertigte Stecker-Endkappe. Andere gedruckte Modelle sind entweder verschiedene Prototypen oder flexible Teile, die sie ergänzen.
PC-Blend Carbon Fiber wurde aufgrund seiner Hitzebeständigkeit, Haltbarkeit und Stabilität schnell zum bevorzugten Material. Mit dem Original Prusa Enclosure ist das Drucken aus diesen fortschrittlichen Materialien ganz einfach. Für einfache Prototypen verwenden sie Prusament PETG. Was die Harze betrifft, so verwenden sie Prusament Resin Tough für die meisten Modelle und Flex für Verbindungen und bewegliche Teile.
Werkstatt voll mit Original Prusa-Druckern
Arthur begann mit dem 3D-Drucken an der Universität. Er wollte die Form und das Gewicht eines Autos optimieren – um es besser zu machen. Anders als die meisten Maker versuchte er es zunächst mit dem 3D-Druck von Metall und wechselte dann zu Thermoplasten – insbesondere zu Prusament Filamenten.
Nach sehr ermutigenden Testergebnissen begannen sie mit einem Original Prusa MK3 und erwarben zwei weitere, um mit der Produktion Schritt zu halten. Arthur hat immer mehr Anwendungsfälle für den 3D-Druck gefunden, so dass sie jetzt auf MK4 aufgestiegen sind und den Original Prusa XL und den Original Prusa SL1S erworben haben.
Arthur hat sich sofort in den Original Prusa MK4 verliebt. „Der Drucker macht alles von selbst. Besonders gut gefällt mir die automatische Erste-Schicht-Kalibrierung“, sagt er. „Die Einrichtung ist einfach, und das macht den gesamten Arbeitsablauf viel einfacher“, fügt Arthur hinzu.
Der Original Prusa XL eröffnete ihm mit seinem großen Bauvolumen neue Möglichkeiten. Er begann, an die Grenzen zu gehen, und macht jetzt fortgeschrittene Prototypen von mehreren wichtigen Autoteilen.
„Ich mag den XL sehr. Er ist genauso schnell und zuverlässig wie der MK4, nur eben größer“, lächelt Arthur.
Und ein Werkzeugkopf wird nicht ausreichen. Er verrät seine Pläne: „Wir haben mit einem Werkzeugkopf angefangen, aber jetzt habe ich beschlossen, einen zweiten zu bestellen, um komplexe Modelle mit löslichen Trägern zu machen.“
Das Team nimmt auch einen 3D-Drucker mit auf die Rennstrecke – ein Original Prusa MK3S+ in einem Gehäuse reist mit AIX Racing um die Welt. Bei jedem Rennen gibt es ein Teil, eine Komponente oder eine Anpassung, die 3D-gedruckt werden muss 🙂
Laut Arthur ist die Zukunft des 3D-Drucks im Formelsport mehr als rosig.
„Es ist nur eine Frage der Zeit, bis alle F2-Teams einen 3D-Drucker haben“, sagt er.
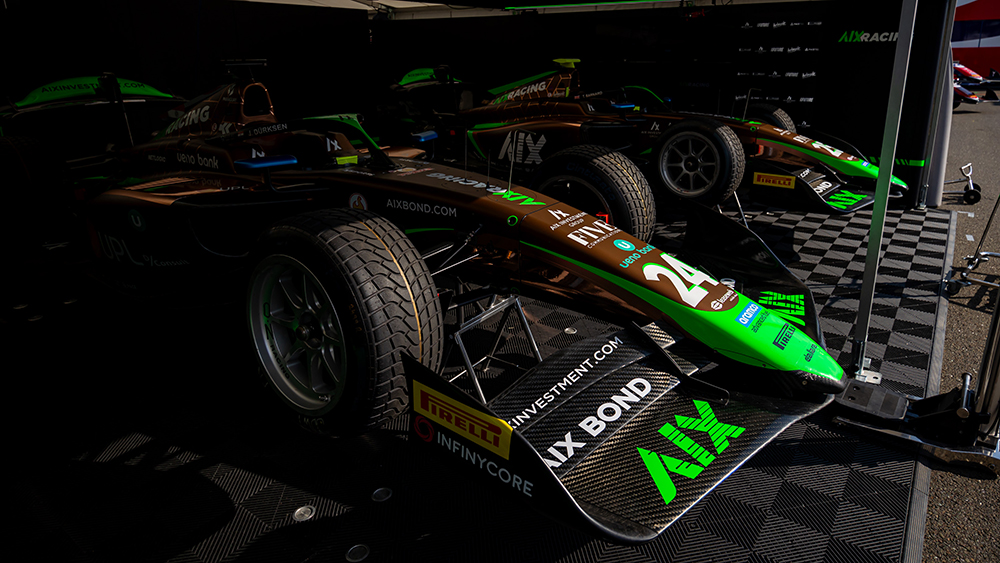
Spielberg (AUT), JUL 27-30 2024 – Großer Preis von Österreich auf dem Red Bull Ring. AIX Racing F2. © 2024 Dutch Photo Agency
Jakub Kmošek, Jakub Fiedler und Štepán Feik
Du musst angemeldet sein, um einen Kommentar abzugeben.