Las carreras de Fórmula combinan emoción y acción. En este mundo altamente competitivo, los detalles más pequeños determinan la línea que separa el éxito del fracaso. Los ingenieros de élite superan los límites de la tecnología y tratan de ser más listos que los demás, mientras los pilotos intentan conducir el coche a la perfección, a menudo arriesgándolo todo. Hoy, nos gustaría ofrecerle una mirada detrás del telón — qué hace el equipo AIX Racing para ser competitivo y cómo utiliza las impresoras 3D Original Prusa para triunfar en los campeonatos de Fórmula FIA.
AIX Racing y Prusa Research han colaborado intensamente durante los últimos años. Nuestras impresoras 3D y nuestros materiales se han puesto a prueba hasta el límite, y han estado a la altura de las expectativas. Hoy podemos afirmar con seguridad que la impresión 3D marca una gran diferencia, incluso al más alto nivel del automovilismo». El ingeniero jefe del equipo, Arthur Rencker, cuenta:
“La impresión 3D nos lo pone todo más fácil,” dice Arthur. Y enseguida nombra las mayores ventajas de esta tecnología: es rápida, precisa in situ e independiente de proveedores adicionales.
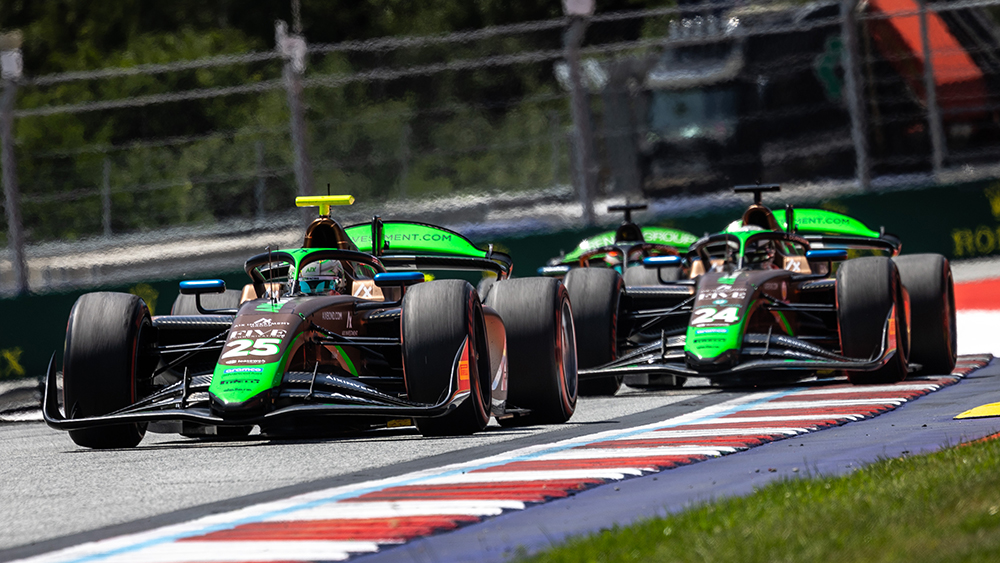
Spielberg (AUT) JUN 27-JUN 2024 – F1 Austrian GP at the Red Bull Ring. Taylor BARNARD #25 AIX Racing F2 © 2024 Dutch Photo Agency
La impresión 3D también ahorra tiempo, del que el equipo no suele disponer. Las carreras de Fórmula se basan en la velocidad, tanto en la pista como en el garaje. Cada año se disputan 14 carreras de F2 y, debido a las escasas oportunidades de realizar pruebas y a las estrictas normas de mejora de los coches, los equipos disponen de muy poco tiempo para realizar ajustes durante la temporada. Las pruebas de pretemporada se limitan a unos seis días, repartidos en dos o tres sesiones de pruebas oficiales. Las pruebas durante la temporada son casi inexistentes, no se permiten pruebas privadas y solo se dispone de unos pocos días de pruebas oficiales.
Además, todos los equipos tienen los mismos coches y motores en la Fórmula 2, la Fórmula 3 y la Fórmula 4. Lo que marca la diferencia es la habilidad del piloto y los ingenieros que ponen a punto las máquinas para sacarles un poco más de rendimiento. Y, como cabría sospechar, aquí entra en juego la impresión en 3D.
Herramientas y piezas personalizadas
La impresión 3D está siempre presente en el taller del equipo – desde piezas funcionales y prototipos diversos hasta herramientas y plantillas ingeniosas. Por ejemplo, Arthur nos mostró un destornillador personalizado impreso en 3D — con un tornillo de diferente tamaño en cada lado y adaptado a la mano de un mecánico concreto. En la pista de carreras, un detalle tan ingenioso como este puede ahorrarte uno o dos segundos preciosos.
Otra herramienta necesaria es un potente refrigerador, que los mecánicos utilizan para enfriar el motor entre vueltas o sesiones. El refrigerador es una pieza de hardware que normalmente puedes comprar tú mismo, pero que se mejora con impresión 3D: en concreto, una pieza de montaje que se ajusta directamente a la admisión del motor del coche o soportes de batería diseñados a medida que pueden alojar celdas más potentes.
Bajo el capó se encuentran otras piezas impresas en 3D, por ejemplo, tubos de flujo de aire de forma única que guían el aire frío a cualquier parte del coche o del motor que se necesite. Esto permite al equipo reaccionar ante cualquier situación durante la carrera. Arthur dice que hacer esto sin impresión 3D sería muy complicado.
La parte del coche que rodea al conductor se denomina «zona de seguridad», y las normas dictan que todo lo que se instale allí debe ser de material autoextinguible. Por ello, los accesorios impresos en 3D se imprimen a partir de Prusament V0. Como este interruptor en la cabina, que… Hace algo que Arthur no quiere que nadie sepa. 🙂
Esto nos lleva a una nota importante: si se pregunta por qué no ha visto ninguna de estas piezas impresas en 3D en la televisión o en los comunicados de prensa, la explicación es sencilla: La mayoría de las piezas o mejoras están cubiertas con cinta adhesiva que imita la textura de la fibra de carbono pulida. Los equipos hacen esto para proteger sus conocimientos técnicos de los demás.
La creación precisa de prototipos ahorra tiempo
El equipo tiene varias impresoras 3D Original Prusa MK4 para la producción de piezas y una Original Prusa XL que se utiliza sobre todo para la creación de prototipos. La principal razón para utilizar impresoras 3D internas es un mejor control del tiempo y los recursos. Durante el proceso de creación de prototipos, realizan muchas iteraciones de sus ideas antes de fabricar la pieza final utilizando otra tecnología.
“Imprimimos las piezas, las probamos, las afinamos, las ajustamos — y solo cuando todo funciona a la perfección, las hacemos en la CNC de aluminio,” explica Arthur.
A menudo, necesitan combinar varias piezas grandes que deben encajar a la perfección, sin dejar lugar a imprecisiones.
Y ahí es donde la impresión 3D les ahorra la parte más valiosa de su apretada agenda.
“Gracias al prototipado preciso mediante impresión 3D, ganamos tiempo extra que podemos dedicar al CNC o al coche,” dice Arthur. Siempre hay algo que arreglar o afinar”, sonríe.
También emplean una impresora 3D SLA — la Original Prusa SL1S — para crear prototipos de piezas pequeñas y muy detalladas, como ruedas de cajas de cambios u otros componentes importantes. Por ejemplo, Arthur nos muestra una tapa de extremo de conector hecha a medida. Otros modelos impresos son prototipos diversos o piezas flexibles que los complementan.
El PC-Blend Carbon Fiber se convirtió rápidamente en su material preferido por su resistencia al calor, durabilidad y estabilidad. Con el Original Prusa Enclosure, imprimir con estos materiales avanzados es muy fácil. Para prototipos sencillos, utilizan Prusament PETG. As for resins, they use Prusament Resin Tough para la mayoría de los modelos y Flex para articulaciones y piezas móviles.
Un taller lleno de impresoras Original Prusa
Arthur empezó a imprimir en 3D en la universidad. Quería optimizar la forma y el peso de un coche para mejorar su rendimiento. A diferencia de la mayoría de los fabricantes, primero probó la impresión 3D en metal y luego se pasó a los termoplásticos, en concreto a los filamentos Prusament.
Tras unos resultados de pruebas muy alentadores, empezaron con una Original Prusa MK3 y adquirieron otras dos para mantener el ritmo de producción. Arthur ha encontrado cada vez más casos de uso para la impresión 3D, por lo que ahora han actualizado a la MK4 y adquirido las Original Prusa XL y Original Prusa SL1S.
Arthur se enamoró inmediatamente de la Original Prusa MK4 . “La impresora lo hace todo sola. Me gusta especialmente la calibración automática de la primera capa,” cuenta. “La configuración es sencilla y facilita enormemente todo el flujo de trabajo,” añade Arthur.
El gran volumen de construcción de la Original Prusa XL le abrió nuevas posibilidades. Empezó a superar los límites y ahora fabrica prototipos avanzados de varias piezas importantes de automóviles.
“Me gusta mucho la XL. Es tan rápido y fiable como MK4, pero más grande,” sonrie Arthur.
Y un cabezal no va a ser suficiente. Nos revela sus planes: “Empezamos con un cabezal, pero ahora he decidido encargar otro para hacer modelos complejos con soportes solubles.”
El equipo también se lleva una impresora 3D al circuito: una Original Prusa MK3S+ en un cerramiento viaja con AIX Racing por todo el mundo. En cada carrera hay una pieza, componente o ajuste que necesita ser impreso en 3D. 🙂
Según Arthur, el futuro de la impresión 3D en las carreras de fórmula es más que brillante.
“Es cuestión de tiempo que todos los equipos de F2 tengan una impresora 3D,“ dice.
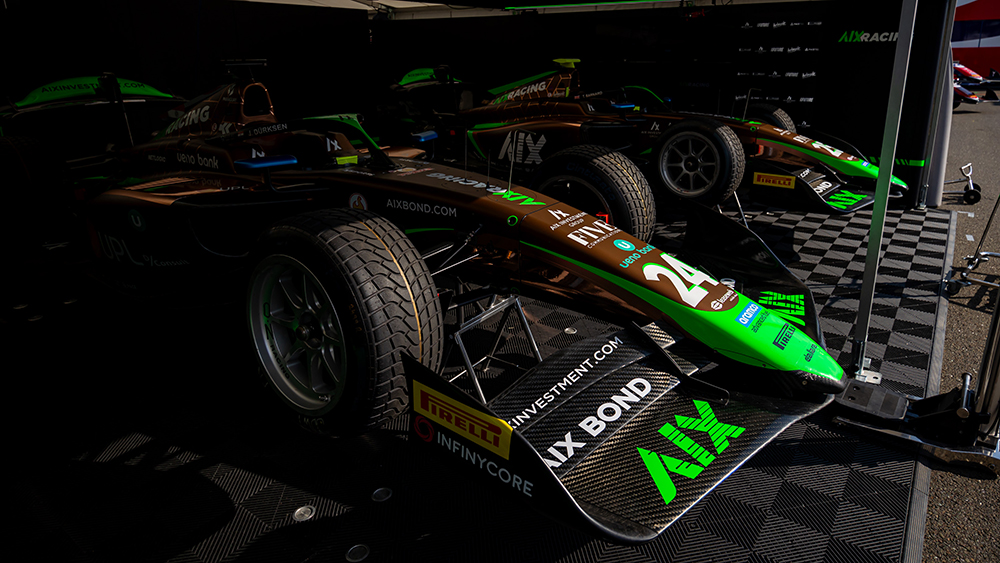
Spielberg (AUT), 27-30 JUL 2024 – Gran Premio de Austria en el Red Bull Ring. AIX Racing F2. © 2024 Agencia Fotográfica Neerlandesa
Jakub Kmošek, Jakub Fiedler y Štepán Feik
Lo siento, debes estar conectado para publicar un comentario.