RC airplane wheels, flexible phone covers or durable GoPro cases – there are some things you can’t (or shouldn’t) print with regular filaments such as PLA or PET-G. However, there’s a group of special filaments that are perfect for this job – flexible filaments! They can be a bit tricky to use, so we decided to bring you this article that will help you get started with these wonderful materials!
Printing with flexible filaments is yet another way to expand your 3D printer capabilities. Unlike most common materials (such as PLA or PET-G), these filaments offer flexibility, great adhesion between the layers and often also elasticity. Printed objects can be not only flexible but extremely resistant to mechanical wear or damage as well. However, there are some downsides, too. Printing these filaments requires a more thorough pre-printing preparation, plus some tweaking and tinkering – in layman’s terms: having some experience with 3D printing is a huge plus.
Our Original Prusa i3 MK3 printer is designed to print various materials, including flexible filaments. However, to help you print these materials, we have rebuilt the extruder to MK3S version so it would be even more flex-printing friendly. You should also download the latest version of Slic3r PE that will automatically update every profile change when it comes out (you can read more here). So let’s take a look at basic qualities and optimal settings for flexible filaments.
There are two types of materials being used for 3D printing: TPE (Thermoplastic Elastomer) and TPU (Thermoplastic Polyurethan). Although having two different names, TPU is actually a type of TPE material; the main difference between them is mainly in shore hardness. Plastics called as TPU are usually tougher, their hardness is somewhere around 60A-90A on the shore hardness scale (see below).
As we have already mentioned, the main advantages of these materials are flexibility, solidity, and elasticity. A great solidity is caused by excellent adhesion between layers. Printed products can withstand a lot of mechanical stress without breaking, which means that flex filaments can be used e.g. for printing spacers or other highly-stressed parts.
Among the main disadvantages are things like very slow printing, poor bridging and stringing. Also, you need to keep in mind that not every model is suitable for printing with flexible filaments and it is necessary to choose carefully what to print. Generally speaking, printing with softer filaments is more difficult. For example, soft TPE filaments tend to detach on the sides from the heatbed. We have the best experience with TPU filaments with shore hardness 92A and 98A (available on our e-shop).
Tips for useful flexible prints
So what exactly can be made with flexibles? We have tried to print several simple models that can be used in everyday life or just for fun. We have also asked our fans on Twitter for some inspiration and we got dozens of cool photos – so check out that link to see more!
At first, we thought it would be a great idea to print RC model tires. They look really good when printed from 92A flexfill, however, they don’t have good adhesion due to filament hardness. Therefore they are more suitable for RC plane landing gears rather than for cars. You can modify the tire softness by changing infill parameters and number of perimeters. When you set it too high, the tires will be too hard and you might lose the key feature of flexible filaments.
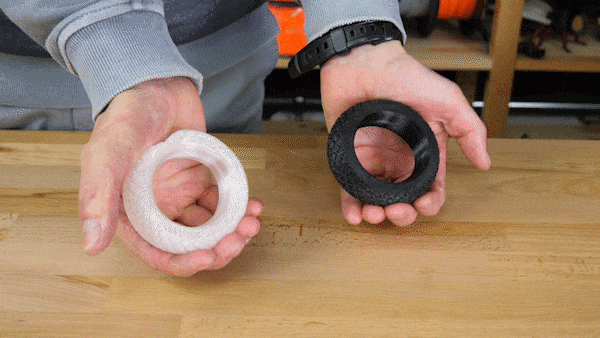
Left: Flexfill 98A with 2 perimeters and 8% infill. Right: Flexfill 92A with 1 perimeter and 8% infill.
Next, we tried to print our own stamp. The result can be quite good if you use a soft filament. The stamp must have a very smooth surface to work properly. Therefore it is important to sand it after printing, or print with contact surface heading down to a smooth sheet.
Many people will appreciate the possibility of printing a protection case for their cellphone or GoPro camera. We tried to use harder and softer filament and found out that both variants work pretty well. Some of the protective cases can’t be printed well without using support material. You’ll have to adjust printer settings or accept the fact that bridging areas won’t be as nice as with PLA or other standard materials.
Print preparation and settings
1) Loosen your idler as much as possible before you start loading the filament/printing. There is a high risk that the filament will tangle around the bondtech if there’s too much pressure on the string.
2) Spread a thin layer of glue on your print surface (regular paper glue stick should work fine). This step is necessary when using the smooth PEI sheet. You don’t need to use glue on powder coated sheets. Without glue, the printed object will be hard to remove from the surface because of a good TPU adhesion and you could actually damage your sheet. Alternatively (for TPE filament), you can print on a regular sticky tape as seen in this video. In Slic3r PE, we have heatbed temperature set to 50°C. That is the optimal temperature for Flexfill 92A and 98A, however, it might differ for other types of filament, for example, TPE doesn’t stick to the heatbed with this temperature.
3) You have to print very slowly, typical safe speed is 20mm/s. Generally, a maximum recommended speed for flexible filaments is 30-40mm/s, because you would risk clogging the nozzle if you set the speed too high. In Slic3r PE we recommend using the „Semiflex or flexfill 98A“ profile. It has an optimal speed set through the maximum volumetric speed (It is set to 1.5mm3/s, that’s approximately 17mm/s when using 0.2mm layer).
4) Keep your filament dry. Flexible filaments absorb a lot of moisture and are more difficult to print with when stored improperly.
How to achieve better-looking prints
1) We suggest setting a less dense infill if you want your object to be more flexible. However, you should add more top solid layers (Print settings – Layers and perimeters – Horizontal shells). As mentioned above, bridging is usually very poor and your model might have holes in it.
2) Set retractions as low as possible. If you struggle to find an optimal value, try to turn them off completely, then raise them little by little. If you set the retractions too high, you risk clogging the nozzle or getting the filament entangled in the extruder. Our Slic3r PE profile includes tested and optimized values, so in most cases, you should keep them that way. It is also important to note that the combination of flexible filament and small retractions causes a lot of stringing which is inevitable. If the printed object is “hairy” or has some leftover strings, you can remove them by heating up those parts very carefully with a flame or a heat gun – be extremely careful so you don’t damage the model or hurt yourself!
3) Raise the recommended hotend temperature to 5°C higher. The nozzle might put up too much of resistance and the printed object could be under-extruded or completely messed up. Keep the print fan turned off.
4) If you need to print supports, set the gap between the layers in Z-axis to at least 0,3mm (in Slicer PE under Print settings – Support material – Contact Z distance). Otherwise, it’s very difficult to remove all of the support material due to high adhesion between layers.
To summarize the possibilities of flexible filament: objects printed from flex are a better fit for practical use rather than for printing beautiful models. However, flexible materials can open completely new possibilities for your 3D printer. We hope that our tips and tricks will help you overcome possible issues and you’ll print something awesome. If you do, don’t forget to share your prints with us – either in the comments section or via social media channels. You can also find inspiration on Twitter thanks to the work of our followers.
コメントを投稿するにはログインしてください。